Optimizing geothermal’s potential with advanced insulative coating technology
As the geothermal market heats up, NOV’s insulative pipe coatings help operators maximize high-temperature drilling efficiency and high-energy heat production.
Tapping into hotter resources can be a major game-changer for geothermal development, resulting in more productive fields and a fewer number of wells to target any given capacity. However, this comes with the dilemma of downhole tools also being subjected to temperatures beyond what they were designed for.
In this guest article written by Michael Adams and Reza Fard from NOV, we learn about insulative coating technology and how this helps keep the drilling mud cool even in very high-temperature environments, thus avoiding temperature-related failure of downhole tools.
Geothermal operators face several challenges in efficiently extracting high-energy heat from deep, hot reservoirs. On the one hand, operators want to minimize cooling of the produced fluids to maximize the geothermal energy delivered to the surface for power generation and other applications. And on the other, they must safely drill into hot rock formations while protecting temperature-sensitive electronics in downhole drilling tools.
A geothermal operator faced such challenges while planning several enhanced geothermal system (EGS) projects, where wells are drilled into deep, dry rock formations at temperatures of 150°C to 300°C (300°F to 570°F). At these temperatures, the drilling muds used to circulate rock cuttings out of the well and cool downhole electronics in the drillstring’s bottomhole assembly (BHA) would get too hot—resulting in tool failures and expensive downtime to pull the string and make repairs.
The operator approached NOV for a novel solution: an insulating drillpipe coating that keeps the drilling mud cooler to protect the BHA from temperature-related failures.
Innovative solutions built on proven performance
NOV’s Tuboscope division has been an industry leader in developing innovative coating products for more than 80 years. In oil and gas applications, these coatings are proven to increase the operating life of tubulars while optimizing each asset’s long-term, profitable production.
Tuboscope’s coating R&D traditionally focused on improving hydraulic efficiencies in the pipe and delivering improved protection against corrosion, wear, and deposit buildup. When the request for a heat-insulated coating came in, researchers quickly added thermal conductivity to their testing criteria.
Thermal conductivity is a measure of a material’s ability to conduct heat (Fig.1). For coated drillpipe in geothermal applications, the lower the thermal conductivity, the better. Low thermal conductivity translates to lower heat transfer rates through the tubing string—keeping the drilling mud cool and retaining more high-energy heat in the pipe on its way to the surface.
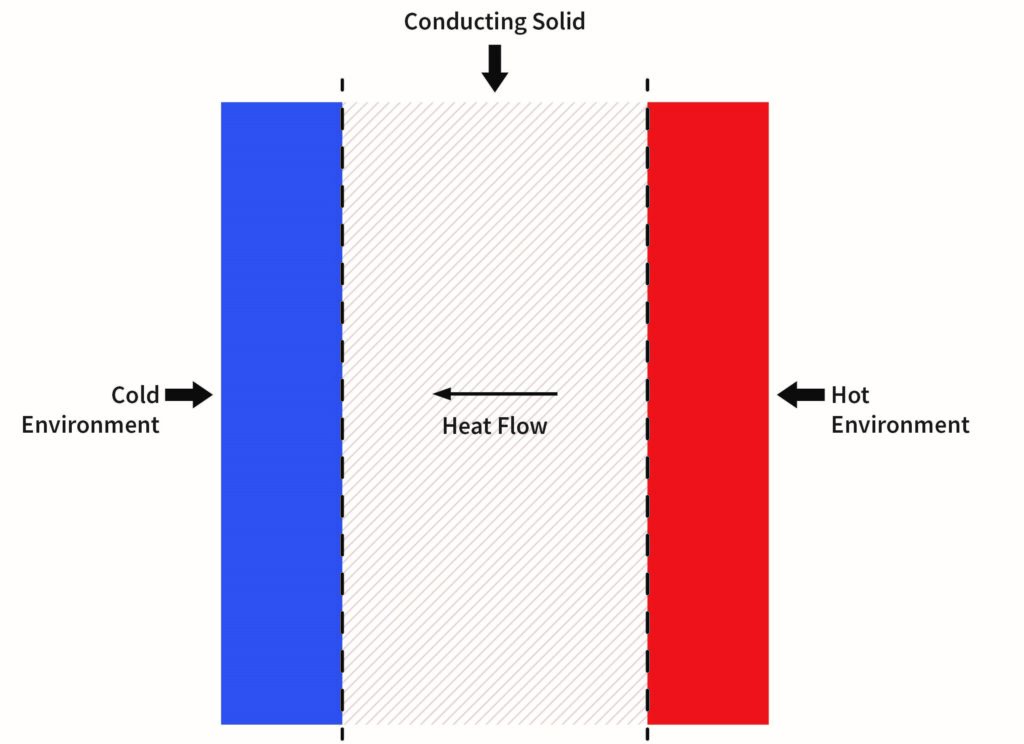
The operator shared the results of modeling work that highlighted the specific temperature-regulation challenges facing their EGS projects. The operation required long drilling strings, including laterals, that would quickly heat the drilling mud above 150°C without any insulation in place. The models indicated that the drilling muds should be maintained below 120°C (248°F) to protect the electronics in the BHA.
Meeting this metric would require a coating with a k value (a standard thermal conductivity measurement) of no greater than 0.5 W/mK. At the same time, the coating would have to maintain the same corrosion resistance and hydraulic efficiency performance of legacy coatings and be applied with minimal thickness to keep costs down.
With the operator’s model results as a guide, the Tuboscope researchers went to work developing a low thermal conductivity coating. Different coating formulations were developed and tested for their thermal conductivity using a heat flow meter that followed the ASTM-E1530-19 standard, the primary measurement of thermal resistance/conductivity for solids (-20°C to 310°C). Each formulation was compared to the measured k value of Tuboscope’s current drillpipe coating, which had not been altered for insulation performance.
The current coating class had an average thermal conductivity of 0.8360 W/mK, which is much lower than carbon steel alone (45 W/mK) but still higher than the operator’s target value. Through iterative formulation adjustments, researchers arrived at a coating formulation with an average conductivity of just 0.1808 W/mK, well below the conventional coating value and the operator’s target (Fig.2).
Additional testing of the new formulation’s physical properties showed the same level of reliable downhole performance as the previous generation of coatings. The insulated coating demonstrated superior impact, chemical, and abrasion resistance, as well as excellent corrosion mitigation properties—all of which helped verify the coating’s robustness in harsh geothermal drilling environments.
The coating applies evenly and smoothly to minimize surface roughness and increase hydraulic efficiencies. A smooth coating surface will help prevent the buildup of scale and other solid deposits while promoting the laminar flow of drilling muds in the pipe. This optimizes mud pumping efficiencies at the surface and provides additional cooling benefits to the BHA downhole.
The new coating delivered these results at an applied thickness of just 20-30 mils (thousandths of an inch), which industry experts familiar with this technology development consider a step-change in performance that no other coating has achieved to date.
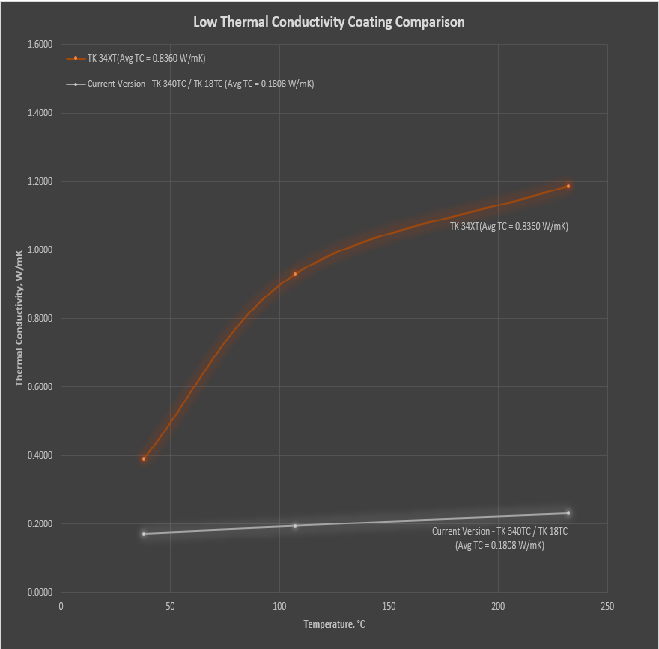
Proving its potential in geothermal and oil & gas alike
The geothermal operator drilled two test wells with the insulated, coated drillpipe, one in New Mexico and another in Utah at the US Department of Energy’s FORGE geothermal research project.
The New Mexico well was drilled a total of 18,000 ft into a reservoir at temperatures up to 250°C (480°F). With the coated drillpipe in the hole, the mud temperature never exceeded 95°C (203°F), well below the operator’s target temperature of 120 °C to prevent BHA damage. The insulated, coated pipe demonstrated similar positive results in the Utah FORGE testing.
Pleased with these test results, the operator purchased an additional string of insulated, coated drillpipe for a commercial geothermal project planned in Europe.
Other geothermal applications for the insulated drillpipe await as operators secure funding and regulatory approvals. But in the meantime, the coated pipe is catching the attention of oil and gas operators who face similar drilling challenges in high-temperature reservoirs of 150°C or higher.
An operator in the Haynesville shale play in Louisiana used the insulated, coated drillpipe to drill long laterals in formations at 220°C (390°F). The drillpipe helped insulate the drilling mud and electronics in directional drilling tools from the high reservoir temperatures while providing a robust corrosion barrier against the hot, corrosive brines in the produced fluids. The operator ordered two more strings of the insulated drillpipe for future wells. Other operators in the region have contacted Tuboscope to apply this pipe in their drilling programs.
Continuing innovations for wider applications
Encouraged by these initial successes, Tuboscope is actively working to deploy the insulated coating technology to more areas and more extreme downhole environments. Oil and gas operators in South Texas, Norway, and other high-temperature regions are asking how the insulated drillpipe environments can improve their drilling operations.
And in the lab, Tuboscope continues to develop next-generation coatings with even lower thermal conductivities, with the aim of helping future geothermal operators drill into deeper reservoirs with temperatures exceeding 300°C. Such innovations will also help operators in shallower, lower-temperature reservoirs minimize heat losses in the pipe to support applications such as district heating, low-enthalpy electricity generation, greenhouses, and hydroponics farms.