How HydroVolve’s percussive-enhanced drilling supercharges drilling performance
The GeoVolve HYPERDRIVE, developed by HydroVolve, uses the principle of percussive-enhanced drilling to reduce geothermal drilling costs.
Reduction of drilling costs, whether through shortening of drilling operations or extension of drill bit lifetime, remains one of the high-impact frontiers for improving the economics of geothermal projects. To this end, innovations that can help reduce drilling costs are of great interest to geothermal developers and may be the key to unlocking deeper and hotter reservoirs.
HydroVolve is one of the companies introducing innovative products to address this area of improvement. In this guest article, Dr. Peter Moyes, Chairman and Founder of HydroVolve, details the working principle of their drilling solution and presents the results of the tests done on their technology.
Geothermal has the potential to supply a significant portion of the world’s energy needs, yet the greatest challenge to scaling geothermal globally is the ability to drill deeper and more efficiently through hard rock formations to reduce capital costs and provide greater return on investment.
Carving deep geothermal wells through thousands of metres of volcanic rock is fraught with technical challenges such as tool survivability in the extremely hot and harsh well environments.
Drilling operations typically need to deal with slow rates of penetration (ROP) – one metre per hour or less is typical – and are routinely halted for days or even weeks when drill bits become blunt and worn and need to be replaced. Such delays, known as flat time, can add millions of dollars to costs.
Rotary drilling vs percussion drilling
At present, two types of drilling method are typically used – rotary drilling and percussion or hammer drilling.
Rotary drilling, by far the most common method to reach the deepest reserves of oil, gas and geothermal, uses two types of drill-bit – the roller cone bit and the polycrystalline diamond cutter (PDC) bit.
The latter has gained ascendancy due to higher ROP and durability yet PDC bits still suffer limited performance in hard rock applications as the required cutter penetration or depth-of-cut (DOC) is more difficult to achieve. Increasing the DOC requires increased weight-on-bit (WOB) to overcome the higher rock strength.
This in turn can increase frictional heat between the bit and the rock face, causing more rapid abrasive wear that shortens bit life. It also introduces other drill string dysfunctions such as stick-slip, helical buckling, lateral instability and high-frequency torsional oscillations, all of which can slow down the drilling ROP and increase the failure rate of the drilling components, thereby making an increase in WOB an unviable option.
The use of percussion drilling is widely practiced in well construction, mining, and construction industries worldwide and utilises a hammer effect to repeatedly deliver a blow through a crushing bit with enough force to break rock into smaller particles.
A fluid medium, usually compressed air, is used to power the hammer tool and to clear away the crushed rock from the impact face and to expose undamaged rock to the hammer. The process is continually repeated at high frequency until the desired depth is achieved.
The performance gains that can be made as a direct result of introducing percussion drilling to a drilling campaign can be significant. As reported by Rodgers et al in 2013, the method delivered the fastest and deepest percussion air hammer run in Australia’s oil and gas history at 24 m/hr.
In practise, however, these air powered percussion tools can only function properly in shallow wells as power loss, wellbore instability, and temperature problems severely limit their use in deep, hot wells.
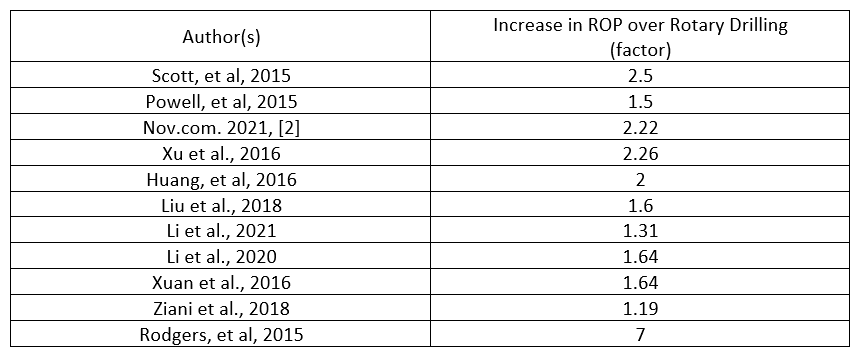
The design principle
Recognising that combining percussion drilling with rotary drilling could be the key to unlocking the potential of deep geothermal, Dr Peter Moyes, a UK-based expert in well engineering, sought to develop a specialist tool that can “supercharge” conventional drilling assemblies – a plug-and-play device to bring all of the known and proven benefits of percussive drilling to rotary drilling without any of the downsides.
Moyes’ percussion-enhanced rotary drilling process relies principally upon the rotary drilling method, using PDC drill bits to fail the rock in rotary shear. To augment the rotating WOB, a controlled cyclic axial impulse is delivered to the bit to induce an impulse force sufficiently large to pre-fracture the rock ahead of the cutter. In essence, it reduces the compressive strength of rock ahead of the bit making a softer, lower strength material to drill. The bit is then able to last longer and deliver much-improved ROP.
The system was required to:
- be powered by the pressurised flow of any known drilling fluid – from fresh water to high density drilling mud laden with loss control material (LCM).
- introduce minimal negative effect to the hydraulic design of the drilling system by avoiding introduction of a significant pressure drop, additional flow volume or flow velocity requirement.
- be operable to 300 degrees C.
- avoid affecting equivalent circulating density or wellbore pressure management.
- avoid inducing unwanted damaging impulse or impact forces to the drilling bottom hole assembly (BHA).
The HYPERDRIVE system
The result is the GeoVolve HYPERDRIVE system, developed by Moyes and his team at HydroVolve, a company based in Aberdeen, Scotland.
The device can be deployed into a conventional rotary drilling bottom hole assembly (BHA) behind the bit and is powered by the flow of drilling mud to hydraulically cycle a percussive axial impulse drive system. This axial impulse force is transmitted through the bit to the cutting structure and onward into the rock where the impulse force pre-fractures and breaks down the rock.
When rotary drilling, it is essential that a constant pressurised flow of drilling fluid is delivered through the drill string to the bit nozzles to cool and wash the bit, to clear cuttings and to transport them to surface. This flow generates a differential pressure between the bore of the drill string and the annulus between the drill string and the well-bore.
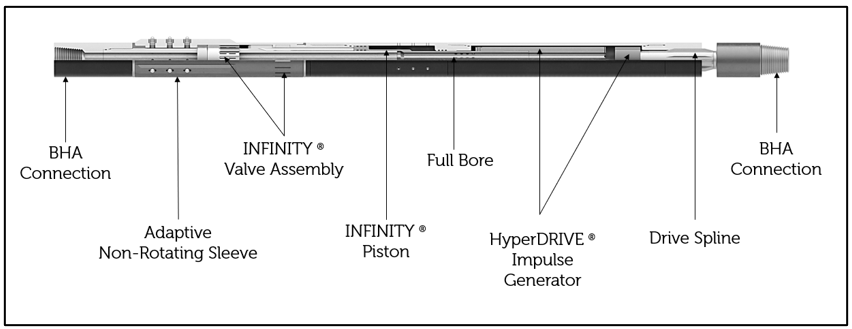
The HYPERDRIVE system capitalises on this differential pressure to power the impulse generator by utilising HydroVolve’s INFINITY engine, a positive displacement reciprocating piston engine featuring an inlet valve aligned to the drill string bore and an exhaust valve aligned to the annulus.
When the inlet valve is aligned to the drill string bore, the piston is exposed to the full differential pressure between the bore and the annulus. The piston is driven under power in the forward direction to create the impulse. When the exhaust valve is aligned to the annulus, the piston is pressure balanced and is spring-returned to the start position.
The TERRABIT
To maximise performance and durability, Moyes and his team asked ZerdaLab, an Aberdeen-based firm with expertise in drilling technology, to analyse the HYPERDRIVE axial impulse load signature and draw on performance data to design and develop a bespoke PDC bit, the GeoVolve TERRABIT.
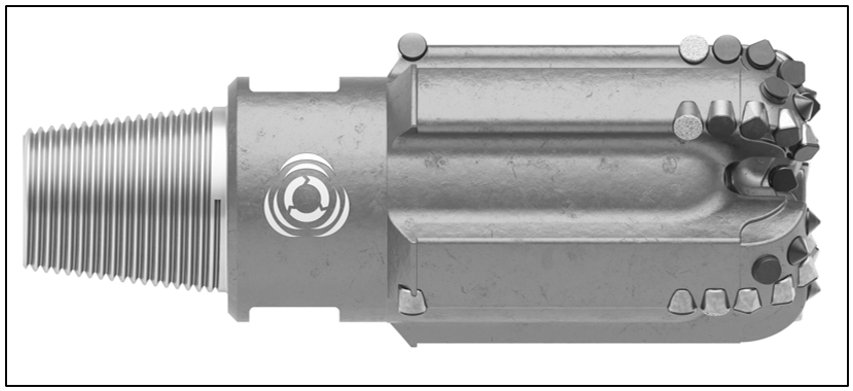
Its features include a profile design to ensure the nose area is well protected to take continuous cyclic axial oscillations and to transmit the HYPERDRIVE energy to the rock. The specialist tool also has a large bit shoulder radius to ensure durability from exposure to high linear velocities in abrasive rock and a radiused cone to allow more space for the extended nose area and provide lateral stability to the bit.
Testing setup and results
Data on the performance of the HYPERDRIVE system in laboratory and field tests were presented at last month’s Geothermal Rising Conference in Reno, Nevada. According to Moyes, the device performed beyond expectations.
“There’s nothing out there at the moment that can survive the depths, the pressures and temperatures in these well bores,” he said. “Over the past 18 months, we’ve launched and deployed a suite of five modular, interchangeable products and systems with performance gains that were hitherto thought impossible.”
All onshore trials were performed at HydroVolve’s bespoke onshore Drilling Test Facility – a test rig featuring a 60-ft horizontal test bed equipped with a 1,200 klbf push/pull capability, a 120RPM, 15,000ft.lb rotary drive system and a 600GPM, 5000psi flow loop. The rig is full instrumented to record WOB, axial impulse load, pressure, ROP, RPM and torque at a data capture rate of 10,000hz.
A 6-inch HYPERDRIVE was fitted with a 6-inch TERRABIT and a series of test programs were performed, drilling in high UCS blue Rubislaw granite to determine the performance characteristics and to define the optimal operating parameters.
The system achieved a gain in ROP by a factor of 2.6 over conventional rotary drilling with identical parameters.
In April and May of this year, field trials were conducted on land operations in continental Europe with three sizes of the HYPERDRIVE system: 12-1/4-inch, 8-1/2-inch and 6-inch.
The trials delivered the fastest ROP ever recorded in an extensively drilled basin; achieved the longest drilled interval ever recorded in an extensively drilled basin; and achieved ROP three times the minimum pre-deployment success criteria
Furthermore, the field trials demonstrated the device’s thermal stability with over 28 days on bottom at temperatures exceeding 220 °C.
One of the trials, utilising a 6-inch TERRABIT, took place in a deep S-shaped profile well with inclination below 20 degrees and total depths in excess of 6000m. The well presented a high contrast in lithologies varying between 5-8 kpsi shale and 22-25 kpsi sandstone reservoir and limestone stringers.
Historically, it was taking from 5 to 15 drill bit runs to drill the 6-inch section with average ROP of 1m/hr.
The field trial was conducted in May 2023 and drilled a total depth of 229m at an averaged ROP of ~2m/hr, more than double the expected drilled distance and triple the ROP expected. It is estimated that had HYPERDRIVE been deployed for the full 6-inch hole section, cost savings for this single hole section would have been in excess of $1,400,000.
Moyes is confident that the field trails prove that the addition of controlled axial impulse to PDC rotary drill bits delivers significant gains in both ROP and bit durability. He points out that HYPERDRIVE works at any depth, introduces no pressure loss and is all metal in construction requiring no elastomeric seals: perfect for ultra HP/HT and geothermal environments.
“Basically, we’re taking existing oil and gas technology and supercharging it for drilling deeper and faster,” he said. “This reduces the overall capital burden on geothermal project development and equally reduces the levelized cost of electricity significantly – particularly important for globalising the opportunity for enhanced geothermal and advanced geothermal systems and delivering geothermal everywhere.”