Andrew Forrest’s big plans for green energy, hydrogen and “real zero” emissions are – slowly – starting to fall into place. One of the most important has been the opening of Australia’s first large scale factory to make green hydrogen electrolysers: All it needs now is customers.
The factory is officially billed as a 2GW facility, but Cameron Smith, the head of hydrogen systems at Fortescue, tells Renew Economy that the capacity is actually much greater than that.
One production line has been opened that can produce 2,920 one megawatt (MW) electrolyser stacks a year, and a second line – depending on demand – could lift total production capacity to double its advertised rate.
“If the orders are in place, we’d have the ability to produce over four gigawatts out of that facility, as it stands today,” Smith says. And demand could grow as the Fortescue technology completes its certification process in Australia, in the US, and other countries.
A capacity of 4 GW would make the facility one of the biggest in the world, but the big question for observers is the ability of the Queensland factory to compete with other electrolyser makers, particularly from China, with some established suppliers such as Plug Power suffering plunging share prices because of concerns about cost.
Fortescue’s technology is entirely home grown. Well, almost. In 2022 Fortescue bought the assets of US-based Exegy, which included a specialist company called Ionix, now known as Fortescue Ionix, which is a leader in the development of hydrogen technologies.
“This all starts and finishes with the membrane,” Smith says. “And Ground Zero globally for molecular chemistry is all around Delaware.
“We acquired what was a relatively small enterprise which has some of the world’s leading technology and IP and patents around membranes. And it just gives us such a huge advantage because we don’t have to rely on anybody else.”
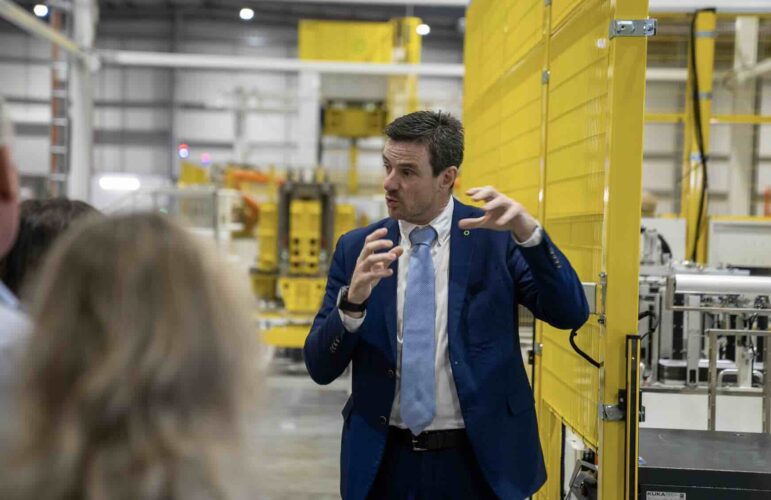
Smith says that IP has been combined with Fortescue’s engineering know-how elsewhere in the company, and in Perth they been working on the “envelopes” and systems that work around those membranes and electrolyser stacks.
“We’ve been able to grow our testing capability really rapidly and the rapid prototyping as well. We have quite literally full machine workshops,” he says.
“So, it’s completely in house designs. We knew early on that we were moving a lot faster than a lot of incumbents and rightly so.
“The day we started this, Fortescue started talking in gigawatts, while a lot of others were sort of scaling from kilowatts to maybe megawatts. So, philosophically, we’ve had a different outlook and I think that’s really been able to allow us to move quite fast.”
Smith says that the cost of green hydrogen electrolysers are not yet where they need to be to “truly rival” fossil fuels. Advances are still needed in materials, and efficiency, particularly the latter because so much depends on how much green power is consumed in the making of hydrogen, and the cost of that power.
“Frankly, the cost of the stack doesn’t matter,” Smith says. “What matters is what the total cost of the system is, and that’s really dependent on water, what the power profile looks like, the level of connections you’ve got to make and whether its grid connected or not grid connected.
“So any cost discussions where people say well where x per megawatt or extra kilowatt, you’ve actually really got to understand the detail the system … these are deeply engineered systems that need to integrate into a broader, broader power grid.”
Smith says Australia has challenges because it does not have the benefit from large legacy hydro projects, like Canada and much of Europe and other countries, and not does it (yet) have the level of support of other countries, such as the US with its Inflation Reduction Act.
That, he says, has meant that Australia projects have gotten smaller.
“So there’s a lot of work for Australia to do to get ourselves in a position where we’re able to put these these mega projects on the ground.
“People have scaled back their initial thoughts where they’re going to do hundreds of megawatts, or gigawatts. And they’ve said, let’s do a five megawatt system and just make sure that we can start to grow the use of hydrogen and the hydrogen economy.
“So we’ve seen a huge spike in the smaller systems, and that’s where we have started look at the engineering work and approvals and feed into much more agile one megawatt and five megawatt systems that would support a refueling station or back to base transport logistics system.”
This is true of one of Fortescue’s own signature projects, a proposed 550 MW electrolyser facility at Gibson Island, near Brisbane, which is looking at opportunities for green ammonia.
But, despite signing a tentative agreement with the giant Bulli Creek solar farm being developed by Genex Power, Fortescue has missed three deadlines for financial closure on the project, with the assumption being that it is about energy costs and logistics.
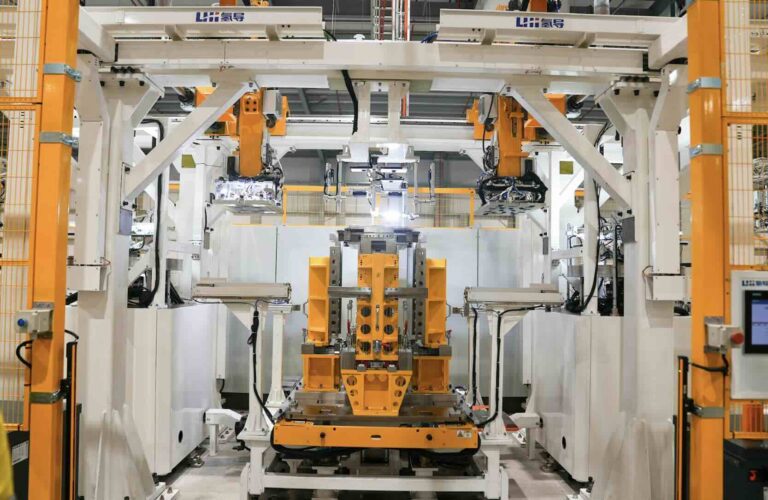
Fortescue is building a range of electrolyser systems at its Gladstone gigafactory, which are known as P1, P5 and P50, which refer to their respective capacity in megawatts.
The company is already committed, with the help of government financial support, to a 50 megawatt system in Gladstone, and is talking to potential customers to sign up for the output of that system.
Fortescue’s electrolyser technology is based around Proton Exchange Membrane (PEM) electrolyser stacks, which turns out to be a good thing because unlike alkaline systems it is much more flexible. That fits well with Australia’s green energy profile, which is based around variable sources such as wind and solar.
Smith says it might take a while for the facility at Gladstone to ramp up to full production, as it depends on the number of customers, including Fortescue.
“We know that we need to be doing (a production rate of) hundreds of stacks by early next year. And then by sort of late next year, we need to be up to the gigawatt scale. But I guess we have just got to be realistic because that’s dependent on orders.”