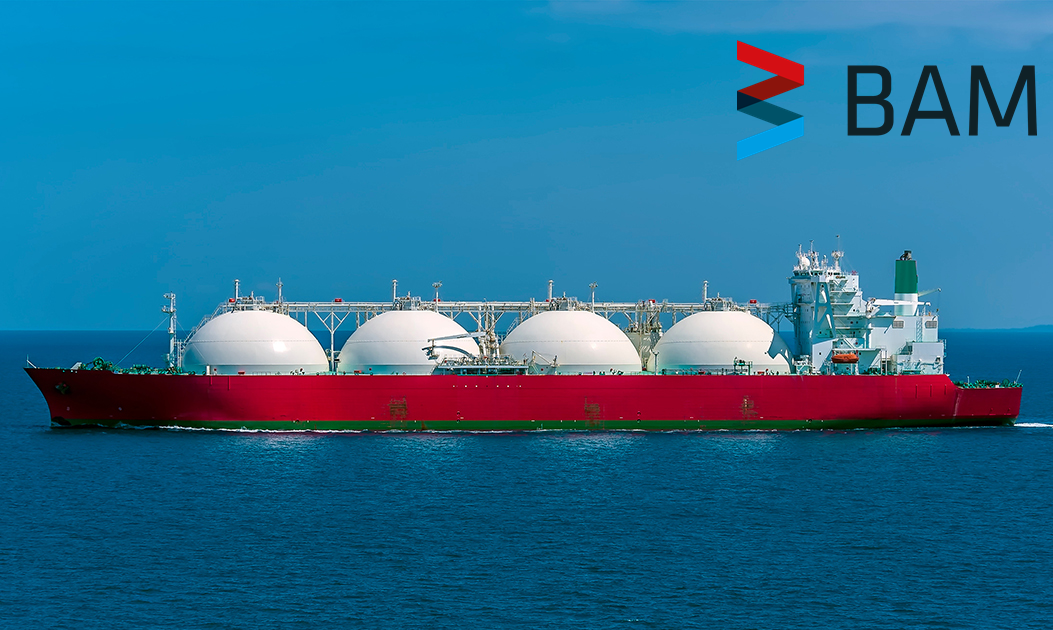
Liquid hydrogen is currently transported and stored using ball storage devices. However, these are not optimal for large-scale use. A European consortium led by the Federal Institute for Materials Research and Testing (BAM) is therefore working on a new, groundbreaking storage concept. The goal is to increase the capacity of suitable containers by 40 times while reducing costs by 80 percent.
Liquid hydrogen (LH2) is transported and stored at minus 253 degrees Celsius because it then has a particularly high energy density. Due to the extremely cold temperatures, thermal insulation is particularly important. So far, the large LH2 storage tanks have been designed in a similar way to the small tanks for liquid natural gas: they have a spherical shape to better withstand the pressure and minimize storage losses. They also have a double wall that is difficult to produce and serves as thermal insulation.
However, ball storage has several disadvantages that make them unsuitable for large-scale use in the hydrogen economy:
- The capacity is currently limited to a maximum of approx. 5000 cubic meters. However, in the future, liquid hydrogen will require tanks with at least ten or forty times the volume, both on ships and for stationary storage. Scaling the tanks accordingly is complex and involves technical risks.
- The production time for ball storage is currently very long at over a year, as many of the processes build on each other and therefore have to take place successively.
- Scaled to the required storage sizes of 50,000-200,000 cubic meters, the outer insulation layer made of polyurethane would have to be several meters long.
In the “NICOLHy” project, BAM is researching new types of storage for liquid hydrogen together with four European partners. The principle of VIP thermal insulation (VIP=Vacuum Isolation Panel, German: vacuum insulation panel) is being tested for hydrogen storage for the first time.
It is known, among other things, from building insulation. With VIP insulation, cold loss or heat input is minimized by a double wall with a vacuum and a filling material made of a highly porous powder. The vacuum and filling material work together and ensure that overall hardly any heat can flow.
This structure makes it possible to achieve sufficient insulation against heat input from outside with VIP insulation measuring just two centimeters. Another advantage: The tanks can be constructed rectangular and, for example, B. can be fitted into the shape of a ship. Compared to previous ball storage systems, the loading space can be optimally utilized.
“Initial results show that the VIP isolation principle can be used successfully to store liquid hydrogen,” explains Robert Eberwein, an expert on dangerous goods tanks at BAM, who is coordinating the EU project. “Overall, the capacity can be almost doubled compared to ball storage, manufacturing costs can be reduced by 80 percent while at the same time increasing energy efficiency and safety. In the project we will continue to research aspects such as sustainability, economic efficiency and safety. Modular storage technology could significantly accelerate the establishment of liquid hydrogen in the German and European energy industries.”
In addition to BAM, the University of Bologna, the German Aerospace Center, the Norwegian University of Natural Sciences and Technology and the National Technical University of Athens are involved in the project consortium.
Source: BAM
Read the most up to date Fuel Cell and Hydrogen Industry news at FuelCellsWorks