Casting Matters — Diving Into Tesla’s Casting Dreams
Or: why Elon Musk is excited about a technology that has been known for such a long time.
Complexity is a vulnerability, and having 1 part instead of 70 single parts eliminates 69 opportunities for something to go wrong. To be more accurate, its 69 times X opportunities, as I will outline in this article.
Read about the innovative pros and cons of large casting structures below, and what they have to do with our nature and Tesla.
Tesla has revealed an innovation for the Model Y, a large casting part, that may sound like a minor technical detail for some — but it is not, and it has huge implications for the entire automotive industry.
An innovate large casting part may be copied one day from the competition if they are able to copy a process no one managed to control before, but the pace of innovation will have already brought the company at that point in time to the next level from testing limits, learning, expanding, and improving. Elon Musk already announced they intend to take the as of today two large casting parts of the Model Y and make them into one.
But what the heck is casting?
“In metal works, casting is a process in which a liquid metal is somehow delivered into a mold (usually by a crucible) that contains a negative impression (i.e., a 3-dimensional negative image) of the intended shape. The metal is poured into the mold through a hollow channel called a sprue. The metal and mold are then cooled, and the metal part (the casting) is extracted. Casting is most often used for making complex shapes that would be difficult or uneconomical to make by other methods.” (Source: Wikipedia)
A special combination is liquid metal as well as a press that forces the alloy into the shape. The key words to remember in that definition are: “complex shapes” and “uneconomical to make.”
When you do casting right, you can cast away 69 single parts that would have caused a lot of complex working steps to make them, and you bring them together into one firm piece that fulfills the required function, be it with dwelling, screwing, clicking, or whatever technology it is. In any case, it’s a lot of effort and work, but also has cost and tool implications. It means an exponential reduction on workload, handling, storing, tooling, maintenance, risk, complexity, shipping, and managing.
In the university, our professor whom we called “3-finger Joe” because he had lost two fingers as a metal worker, taught to us that touching a single part one time cost you $1, and if it’s 70 parts, it would be $70 less just by moving them one time from A to B within your plant.
Congratulations, with your new casting part, you have just realized an awesome handling cost reduction of 98%, and that’s just handling, not even manufacturing, connecting or linking, assembling, or dwelling. Now multiply this by, let’s say, 10,000 vehicles a week produced in Fremont, and don’t forget to add labor, tooling, maintenance, energy, space, time, and material costs.
You get the picture – we are talking about big money here, and huge time and space savings too, because you don’t need all the tools, people, and robots any more. Small pennies saved per piece and per activity in mass production are big dollars at the end of the process. That’s why Elon Musk said once they are hunting for the pennies here and there as they scale up exponentially.
But let’s not fool ourselves, because on the other side of the equation you have the costs for the largest casting press the world has ever seen, with new requirements for the building it stands in, an uncertain new process with a new likely unproven alloy, high material waste at start, high energy cost, as well as maintenance and expensive specialized labor. I predict at the start the costs are higher than previously, but that’s just the start, and afterward costs do decrease exponentially, leading to increased savings.
This is called process costs, or the innovation to make an innovation work. Some of you may have heard Elon Musk saying that mass production is hard. As a production engineer, I can tell you that he knows what he’s talking about. Innovation works great on paper and in a controlled environment, in a test environment, but a few thousand times a day in production is a completely new challenge and an order of magnitude harder to accomplish.
For that reason, those changes are taken with caution, as they can backfire, losing you time, money, and reputation, like we have seen with the Alien Dreadnought attempt to automate almost everything in the production process in Fremont, including, for instance, cabling in which robots had a hard time fighting with flexible cable structures that are easy to handle for a human but too unpredictable in their movements for a robot.
Throwing away a known working process does not happen in the incumbent automotive industry unless you can prove the savings right at the start. Instead, they prefer continuously optimizing a working process. When you need to prove it with a new building and a large casting press that does not yet exist, you cast the idea away.
One of my hardest challenges as a writer is not writing thoughts down, but throwing thoughts away simply because they don’t fit into the story I am trying to tell. To trick myself out of the dilemma of being unable to throw sentences away that I fell in love with, I copy them in another document and store them away pretending I can reuse them one day in the future. A day that never comes. It’s my private garbage dump of brilliant thoughts. Don’t ask.
The same is true for production technology and inventing. Only if you are willing and able to throw away what you have optimized and worked on sometimes for years will you make progress and move forward. Most people and organizations are unable to do this because they are a master of that small but excellent part and have a famous technology for how to attach it. Perhaps they have not taken a step back for decades to look at the bigger picture and reconsider if the optimization makes any sense today. For that reason, the way an old process goes away is often from the people attached to it going away.
Just look at your own household, in your storage room and garage, and be honest to yourself what you still have but should have thrown away years ago. It’s growing because you can’t let go what once worked so nicely and is full of memories. Memories are our weakest point, but that’s another story to tell.

The casting technology as described is a one-step process that enables the manufacturing of complex parts that otherwise would take very long and are costly to manufacture, and it has limitations in its size and in quality, to name just two matters. Casting allows low-cost production of parts that have complex shapes due to required technical parameters. Casting’s material usage is low because you can form shapes you can’t make easily, if at all, with traditional techniques. It is fast and looks great, but the process is only used for small parts since larger parts often result in incomplete structures, inclusions, stressed material, or other errors that can’t be repaired. Therefore, you have to throw the whole piece away.
A key challenge of casting large structures is not only the gigantic dimensions of a large press to develop enough force, but also an alloy that on the one side fills the mold fully as required but provides on the other hand the strength you want in your vehicle. The vertical integration of Tesla using expertise from SpaceX engineering with a new alloy is a key element to solve that challenge. No other automaker essentially has a space exploration arm working hand in hand with it. In that respect, you can consider the Model Y to have been engineered by rocket scientists. It won’t be able to fly, but it shares technology with rockets no other vehicle has on the market. So, feel free to make a bumper sticker on the back of your Model Y: “Engineered by SpaceX.”
Casting is an attempt to engineer structures we find in nature, and that has good rationale.
Nature has been build plants optimized over thousands or even millions of years for optimal strength, low usage of material, and high energy efficiency. Take an example from nature and you will learn a lot. As an engineer, you can learn how to better reduce materials, and thus costs, by making strength and efficiency exponentially better. Then the problem is how to manufacture it with existing technology, which is sometimes not an option at all, or may be freakin’ expensive and therefore uneconomical.
An entire science movement developed out of discoveries that started in the 19th century after photographers first took magnified photos of plants and realized not only how beautiful they are but later also that the structures are not just random or made to be beautiful, but have structures with concrete purposes.
They are developed through continuous optimization, offering functional masterclasses humans are not even near able to understand. It turned out that the strength for instance from certain grasses and plants is unprecedented and resists against stress, pressure, and different forces by factors better than the best available steal, with less material usage. People have thus realized that in nature form follows function, and that if humans could learn from it, a lot would be possible no one ever believed achievable before.
Later, some of the findings in nature were used for building better bridges or houses, and in the 20th century some discoveries even made it into in the aviation industry. However, the rather arrogant belief that humans and engineers know what works better than nature — as well as economic, technological, and material restrictions — limited usage and put this into a corner that today would likely be called nerdy or maverick. That science in architecture is today called bionic, and it is underestimated in its value for humankind.

Even though the technology needed to manufacture such things was either very expensive or simply not available, material science has developed in recent decades quite significantly and continues to do so, opening new opportunities. That situation remained and did not change much until today, when for instance shapes are now possible to manufacture with 3D printing. Technologies like printing, gluing or casting, to name a few, are promising candidates for mass production of complex shapes for the automotive industry and are step by step making their way into our vehicles.
This is not a cooled gearwheel or any other metal part of a vehicle or engine on the right, but a picture from a plant that optimized lowest usage of material and combined it with highest possible strength, functionality, and lowest cost of energy.
To get rid of material in places where it is not needed for the required function is one challenge, but to understand where material we use today is useless is another one. To put a functional structure into work requires getting rid of material around what some call “energy lines.” It is the part of the structure that does the work and all the rest is obsolete material. If you manage that, you achieve a masterclass in efficiency no one ever thought possible. That’s true for architecture, building planes, as well as building vehicles and many other things.
To produce this structures in masses for the automotive industry would improve efficiency, cost, functionality and abilities by order of magnitudes while keeping the passenger safer than ever in an accident. The nature is our teacher how to do something best but we insist to ignore her and pretend we know better.
For vehicles where weight of material is critical to the economy of the business, like in rockets, you find more expensive production technology and material use, but it never makes it into mass production like passenger cars because of costs. Instead, most of the efforts to optimize went into fuel and engine efficiency to drive more energy out of a gallon. Instead making the chassis better and more efficient, the opposite happened, and they are now on average heavier than ever in the past, consuming more and polluting more.
Many wars have been fought and many people killed to keep gas prices low in order to protect a business model where an industry can accept the rather incredible situation that a few tons of metal are used in combination with a gas that burns and pollutes our environment and us to transport on average 1 to 2 people from point A to B.
That’s the world we are living in today, and the low oil prices we see these days are a treat to that industry, because the producers, refiners, and trillion-dollar industry that builds products out of it face the risk of going out of business thanks to solar and wind energy cost that are already lower and electric vehicles. Today, battery electric vehicles are better and lower in total cost of ownership (TCO) than internal combustion engine (ICE) vehicles. It’s a money business in which the cost of nature and raw materials from it — like water, air, and earth — have no price but are considered to be provided “for free” like a gift. Nothing in life is for free, and nothing from nature is a pure gift. Sometimes you pay sooner, sometimes you pay later, but you always pay.
One way to be smart is to learn from nature, and by doing that, also protect it. If we can with our energy consumption move closer to how nature is doing things, we will save a lot of resources. We see this happening with attempts to copy the “cold fusion” energy generation that is happening in our sun. It’s a big goal and no one knows if it will ever succeed, but there are other objectives we can accomplish if we try. Two of them are material science and improvements in manufacturing technology.

Right now, manufacturing is almost done like tooling in the Stone Age, where you waste a ton of material to produce a part that barely fits your needs. You use a stone to work on a stone and have as an end product a rather rough knife that is too heavy and not really fit for purpose. We wasted a lot material to produce it and the tool we got does its purpose somehow but is far from perfect.
The same we do today with metal works for mass produced vehicles, where we design dimensions that are way too large and heavy. If nature did what humans do, we would not be on earth and the planet would be without life.
In nature, everything that is not required is basically just not there. You don’t find grass, plants, and trees that have an unnecessary high amount of material wasted, because why should they?
The efficiency and smartness of organic structures around us are amazing and we should learn from them to be better instead of ignoring them and arrogantly not even investigating how bad we are versus how good we could be. It’s time to develop the ideal even if we know that today we won’t be able to produce them in large masses because, for instance, the production technology or required material is missing.
Since humans for many decades have been able to measure exactly what force a vehicle part should be able to manage, they could design a part like in nature, but producing it would be very expensive and take too long a time. This is the moment when new production technology comes into play and can help.

3D printing and casting are just two examples of many that are not used for larger parts but could be to get closer to perfection. Instead, the perfect is declared the enemy of the good and improvements are not made in the incumbent automotive industry since a working process is available — although old, outdated, and very inefficient. If marketing convinces consumers successfully to pay the price, who cares?
Casting and 3D printing are manufacturing technologies that allow material- and cost-efficient production of complex structures you find in nature with the unique combination of higher strength, higher durability, and lower material usage. Those aspects together make them lower cost too.
If you want to identify a casting structure, you don’t have to be an engineer. Just look for a structure that looks somehow organic in its shape and different than all others.
Consider the casting technique as if Hercules slammed with all his power a sledgehammer on a metal block that by the applied force melted into the mold underneath like magic. That’s mainly the process, while Hercules is in this analogy the largest heavy press you can get. It is so heavy that it escapes the imagination of a human mind. “As big as a house” does not describe by any means the irrational force of 6,000 tons that it creates. The pure force alone will create a long list of problems and challenges to solve.
Since I am one of the very few glassblowers by education left in Germany, I know how it feels if a liquid material flows into its form without any stress. It cools seconds later if certain conditions are achieved and takes the desired form naturally. Since a heavy press hitting metal like you have never seen before is certainly not without stress, it is important to understand that the metal alloy is liquid and flows into the mold driven by the force of the press, where it cools down and takes the intended form. That’s important because, if metal cools down in a shape it’s forced into, you have an inner stress that you won’t be able to see but that can cause the product to break at a later point in time. It’s not sustainable and includes a quality, durability, and safety risk.
To avoid that risk, Tesla was able with help from SpaceX engineering to develop a new innovative alloy that is combining the required specifications of enough liquidity while melting at a low temperature point to fill a large mold completely without exception or issues (like bubbles or exclusions), thus cooling down without stress and providing strong metallurgist crystalline structures in required places that are exposed to force and energy in the vehicle.
Consider metal to be built out of different small cells that look crystalline. If they are fine and homogenous, you have a strong part, but if they are heterogeneous with small and large structures, you have a weak one. To achieve that, you have to have an alloy that is able to combine these requirements, and that was only possible to manufacture with help from SpaceX experts based on their experience with alloys of different rockets and turbines. These are experts who are used to dealing with requirements a vehicle engineer has never seen before. This is beyond vertical integration and a unique advantage of Tesla — having access to diverse expertise that Elon Musk can bring together if needed.
3D printing, to give a second example, helped to continue the production of the “octovalve,” as we can see in one of the teardown videos from Munro & Associates. Because of a bad initial design, they had something missing in this place. Usually, you would have to stop production and start again to build a new form. The production line would stand still and wait if you had no buffer with spare parts. 3D printing enabled Tesla to fix the issue quickly and continue production by producing a seamless addition to an existing plastic part. This is cost avoidance that helped to achieve high gross margin and profits in Q1 2020.
That shows how important manufacturing and engineering technology can be for the success of a company. What 3D printing allows is building structures that traditional techniques are unable to manufacture unless you accept a massive effort that is very costly and in most cases slow.
Both technologies enable an organic-looking structure that you can see in the pictures of the underbody of the Model Y that show what look like large cells. They make it look like it’s grown from nature, comparable to the pictures of horsetail architecture above from Karl Blossfeld from 1920.
If you go into your garden, cut a plant, and put it under a microscope, you will be surprised to find similar structures. They are not a success by coincidence, but by purpose and millions of years of iterative improvements.
Elon Musk highlights casting as something he is very excited about, and I share his excitement, as it’s a true game changer.
When it comes to eliminating parts via casting, size matters. Tesla having reduced parts from 70 to 2 from the rear underbody of the Model 3 to the Model Y is amazing already. Implementing a planned reduction from 70 parts to 1 is an incredible innovation and improvement no other automaker in the world is today able to do.
To do that for the entire 3rd of the underbody of the Model Y is a worldwide record by a large margin. Elon Musk: “No casting of that size has ever been done before.”
The implications of casting are illustrated in Tesla’s stock price to some degree, which so far in 2020 increased from $418 to $701, while all other automakers saw their market capitalization fall significantly.
Casting in that size is another invention no one can copy since no one has the technology or the alloy to do it, and with that approach Tesla moves a step closer to a fully automated factory in which the production speed can be dramatically accelerated, like in the original vision of the Alien Dreadnought.
If you produce faster, the average cost per vehicle goes down, and with that you create another moat.
Engineering is magic, like nature is.
Have a tip for CleanTechnica? Want to advertise? Want to suggest a guest for our CleanTech Talk podcast? Contact us here.
Latest CleanTechnica.TV Video
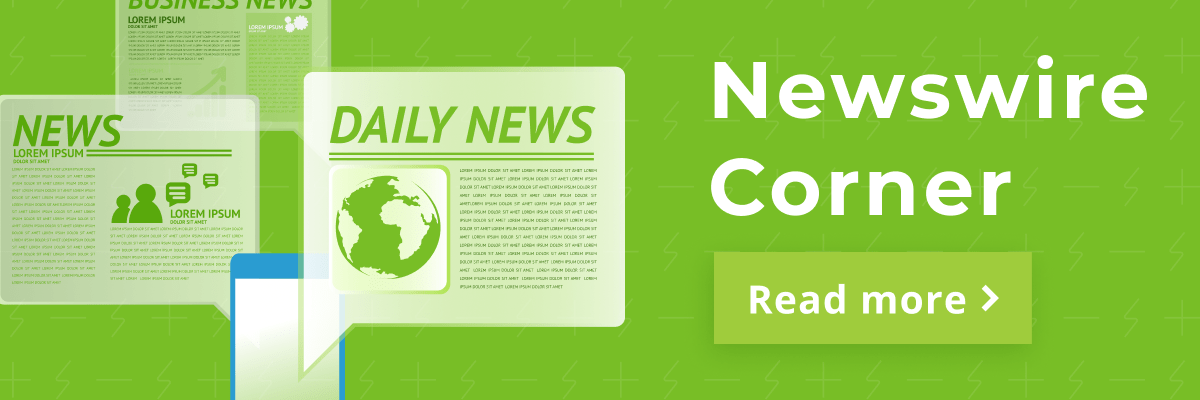
CleanTechnica uses affiliate links. See our policy here.