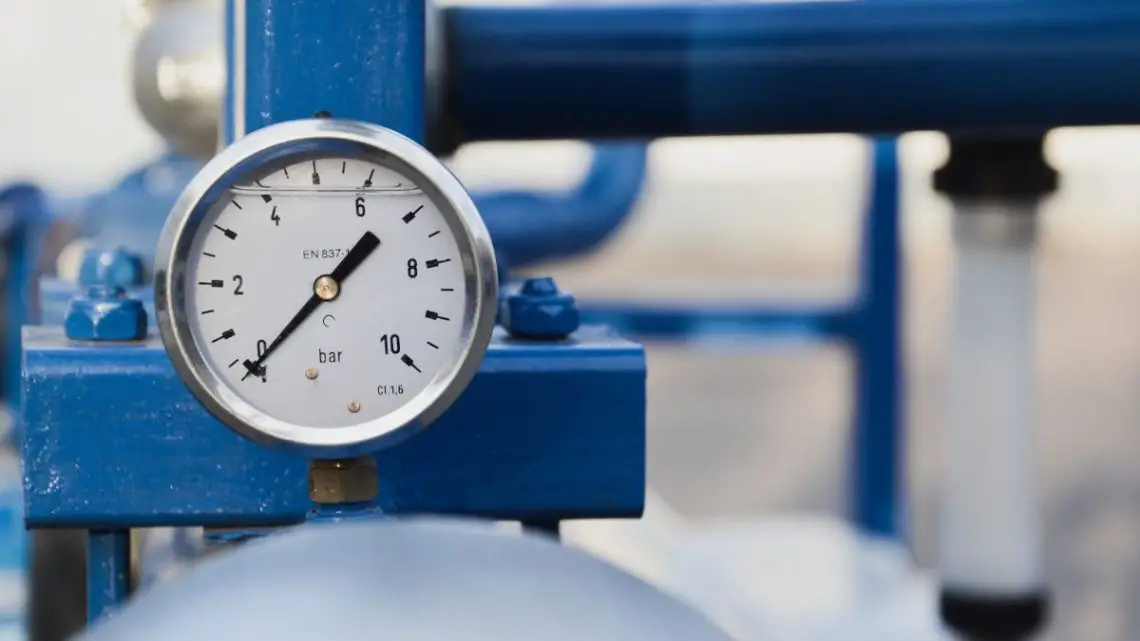
Pressure Sensors Are Critical for Heat Exchange Stations
November 6, 2023Heat exchangers are ubiquitous with modern industrial and residential appliances. They are used in boilers in power plants, swimming pools, and HVAC units. These structures allow two substances to simply exchange heat without mixing. It can be a water and gas setup such that hot gas goes through a pipe, gradually heating the water that surrounds the structure.
It can also be a gas furnace, blower, and ductwork setup where heated propane or natural gas is combined with indoor air and distributed through the ductwork to warm different sections of a building. Still, it could also be an evaporator, compressor, refrigerant, and fan setup where the refrigerant takes heat from outside or inside the building as it moves through the ductwork with help from the components.
In any case, you will need to install pressure sensors to help monitor and control the system, be it watching for clogs in air filters, measuring airflow and controlling fan speed, monitoring water flow from tanks, etc.
What is a pressure sensor?
A pressure sensor is a device used to measure the pressure of fluids and generates a useful output signal proportional to the force being applied by the fluid over an area. The signal can be used in various specialized control and maintenance protocols.
Depending on the working principle, there are various types of pressure sensors, including strain gauges, which use spring contraction and expansion, piezoresistive sensors, piezoelectric sensors, capacitive sensors, vacuum pressure sensors, manometers, etc.
These setups detect mechanical force and generate a proportional electrical or voltage output, which is then scaled into a useful signal for maintenance and alert systems.
Naturally, the signal output changes as the pressure being measured changes. These measurement devices have lots of applications, including in heat exchange stations. Here’s a look at how:
Measuring differential pressure in air filtration systems
Air filtration systems work in tandem with heating and cooling to ensure ambient air inside a property. However, sometimes, this system can get dirty or become clogged, leading to decreased efficiency. Insufficient airflow due to clogged filters can cause evaporator coils to freeze and start leaking.
A differential pressure sensor can allow you to detect a clogged air filtration system and remedy the situation before the filters start dripping or developing molds.
Apart from clogged filters or blocked air flow, another common problem is heating leakages due to cracks, holes, hatches, and insufficient insulation. Air leaks can be a migraine-inducing issue when you are shelling out for heating but don’t see where the heat is going.
Basically, differential pressure sensors estimate the difference in pressure at different points in your HVAC system and trigger warnings to clean your ductwork in case of clogging. You can also use the data to locate areas that need sealing to optimize insulation and prevent heat loss.
Measuring indoor airflow and controlling fan speed
Pressure sensors can be installed in the return air duct of an HVAC system to measure the difference in pressure between outdoor and return air. This measurement is a good indicator of the amount of airflow through the HVAC and can be used by the controller to adjust the damper position or fan speed and achieve demand-controlled ventilation (DCV). Basically, DCV is when ventilation rate is adjusted to match the home’s ventilation needs and actual occupancy.
Alternatively, you can use pressure sensors for variable air volume. This is where sensors are installed in the air supply duct to measure the difference in air pressure between the room and the duct then signal the controller to adjust the damper position so the room receives just the right amount of airflow needed to keep the temperature at a desired level.
Another way to use pressure sensors is to measure the drop in pressure due to friction and other factors as air moves in the ductwork and HVAC components. Once the amount of drop in air pressure has been established, the fan speed can be adjusted to account for the effects of friction and other factors, thus achieving desired air pressure in the ducts.
Overall, using pressure sensors to optimize fan speed based on ventilation requirements helps cut power wastage and extend fans lifespan since they’re triggered to work hard only when needed.
Detecting wear and tear issues
Apart from helping monitor and control airflow, pressure sensors can help detect wear and tear in the air supply duct and HVAC components if used properly. For example, you can use them to measure air pressure drop across filters and indicate when to clean dirty filters or replace them entirely.
You can also use them to detect air leaks in the ductwork by measuring the difference in air pressure outside and inside the ducts and use the data to determine the location of leaks in the system. Generally, if the pressure difference is massive, there’s a leak.
You can also use sensors to monitor pressure drop across your fan and determine the presence of wear and tear. Basically, old or worn-out fans won’t move air as efficiently as they once did. Therefore, a massive pressure drop probably means you have to get new fans.
Another part where you can use pressure sensors is on the compressor valves. These compress the refrigerant into superheated vapor that then moves into the condenser, turning into a liquid before losing heat as it moves through the operator. However, compressor valves can become inefficient due to wear and tear. Installing pressure sensors on the low and high sides of the compressor can help detect wear and tear. The sensors simply measure the pressure difference on the low and high sides. If the difference is too high or too low, the compressor valves may need replacing.
To cap it, pressure sensors are essential in heat exchange station operations. From monitoring and controlling fluid flow rate to detecting clogging, air leaks, and mechanical issues, your system could do with one of these intuitive devices. MicroSensor Corp manufactures a variety of pressure sensors for different applications. We adhere to ODM and OEM standards and work with customers to ensure products meet the requirements of their specific projects. Go to our main page for a first-hand look at our products, and feel free to let us know what you require exactly so we can help.