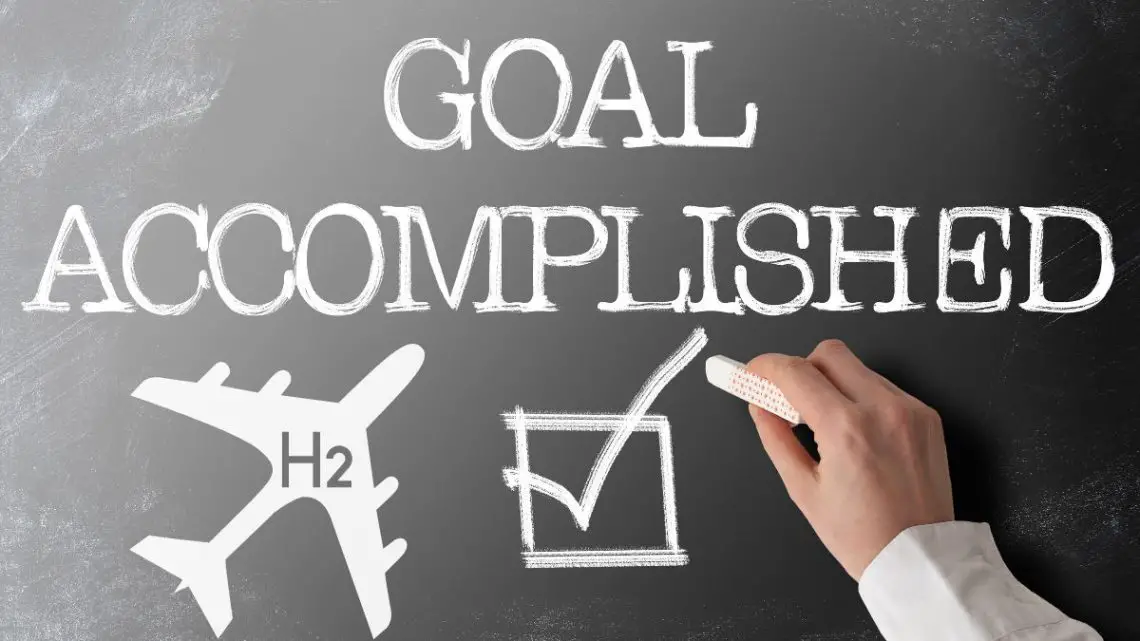
CAeS accomplishes aircraft hydrogen fuel cell integration
March 19, 2024Cranfield Aerospace Solutions has announced successful H2 design integration into a plane
A recent announcement from Cranfield Aerospace Solutions (CAeS) shared that the company has achieved the successful integration of its hydrogen fuel cell technology into an airplane nacelle.
Sustainable solutions for the aviation market
The CAeS stated that the center of its focus is in developing an aviation market hydrogen fuel cell drive train to be certified, safe to use, and commercially viable. In its announcement, the company described how it adapted its tech for aviation applications and how it can function to overcome some of the primary challenges in this area.
The system is 240kW and thereby provides 110 percent of the power of the aircraft engine it was replacing. It was integrated into the plane’s nacelle and placed the spotlight on how the CAeS technology worked to overcome some of the top challenges to H2 integration.
Challenges to hydrogen fuel cell integration
The first main challenge faced by the design team at CAeS had to do with being able to work with the limited space within the nacelle. It was, after all, quite limited, but was still required to hold the hydrogen fuel cell in addition to its cooling equipment, electrical components, and cable and pipe routing.
The forward nacelle
The system itself was stored within the nacelle’s forward section. The electric motor, inverters, controllers, pitch control unit, the system’s Balance of Plant (BoP), and all the various cooling, cabling and routing systems were also worked into that same space.
The rear nacelle
The rear nacelle held the high voltage power distribution system and ground power interface. Each of those required their own cooling as well and came with its own unique challenges.
Additional components
Beyond the nacelles, there were also components mounted around the primary landing gear. Those included the hydrogen fuel cell system (HFCS) heat exchangers. Within the HFCS heat exchangers was the necessary pipework for the cooling system.
According to the CAeS team, each part of this integration needed strategic planning, iterative design, and tight collaboration with its Reaction Engines partners. It was in this way that they could be confident that the design would offer optimal performance.
FAQs for the Article on Cranfield Aerospace Solutions’ Hydrogen Plane Integration
Q1: What was the recent announcement from Cranfield Aerospace Solutions about? A1: Cranfield Aerospace Solutions (CAeS) announced the successful integration of hydrogen fuel cell technology into an airplane nacelle, marking a significant step towards sustainable aviation solutions.
Q2: What is the main focus of CAeS in terms of aviation technology? A2: The main focus of CAeS is to develop a certified, safe, and commercially viable aviation market hydrogen fuel cell drive train.
Q3: How powerful is the hydrogen fuel cell system developed by CAeS? A3: The hydrogen fuel cell system developed by CAeS is 240kW, providing 110 percent of the power of the aircraft engine it was designed to replace.
Q4: What were the challenges faced by CAeS in integrating the hydrogen fuel cell into the plane? A4: The primary challenge was accommodating the hydrogen fuel cell system within the limited space of the nacelle, along with its cooling equipment, electrical components, and necessary cable and pipe routing.
Q5: Where in the nacelle is the hydrogen fuel cell system stored? A5: The hydrogen fuel cell system and related components, such as electric motor, inverters, controllers, and cooling systems, are stored within the forward section of the nacelle.
Q6: What does the rear nacelle contain? A6: The rear nacelle houses the high voltage power distribution system and ground power interface, each requiring its own cooling solutions and facing unique challenges.
Q7: Were there any additional components installed outside the nacelles? A7: Yes, additional components, including the hydrogen fuel cell system (HFCS) heat exchangers, were mounted around the primary landing gear, complete with necessary pipework for the cooling system.
Q8: How did CAeS manage to overcome the design and integration challenges? A8: CAeS managed to overcome these challenges through strategic planning, iterative design, and tight collaboration with its partners at Reaction Engines, ensuring optimal performance of the design.
How Hydrogen Planes Work
Hydrogen planes utilize hydrogen fuel cells to generate electricity, which then powers the aircraft’s engines. Unlike traditional fossil fuels, hydrogen is a clean energy source that only emits water vapor and warm air as byproducts, making it an environmentally friendly alternative for aviation. The integration challenges mainly revolve around storage and efficiency of the hydrogen fuel cells, as well as adapting existing airplane structures to accommodate this new technology.