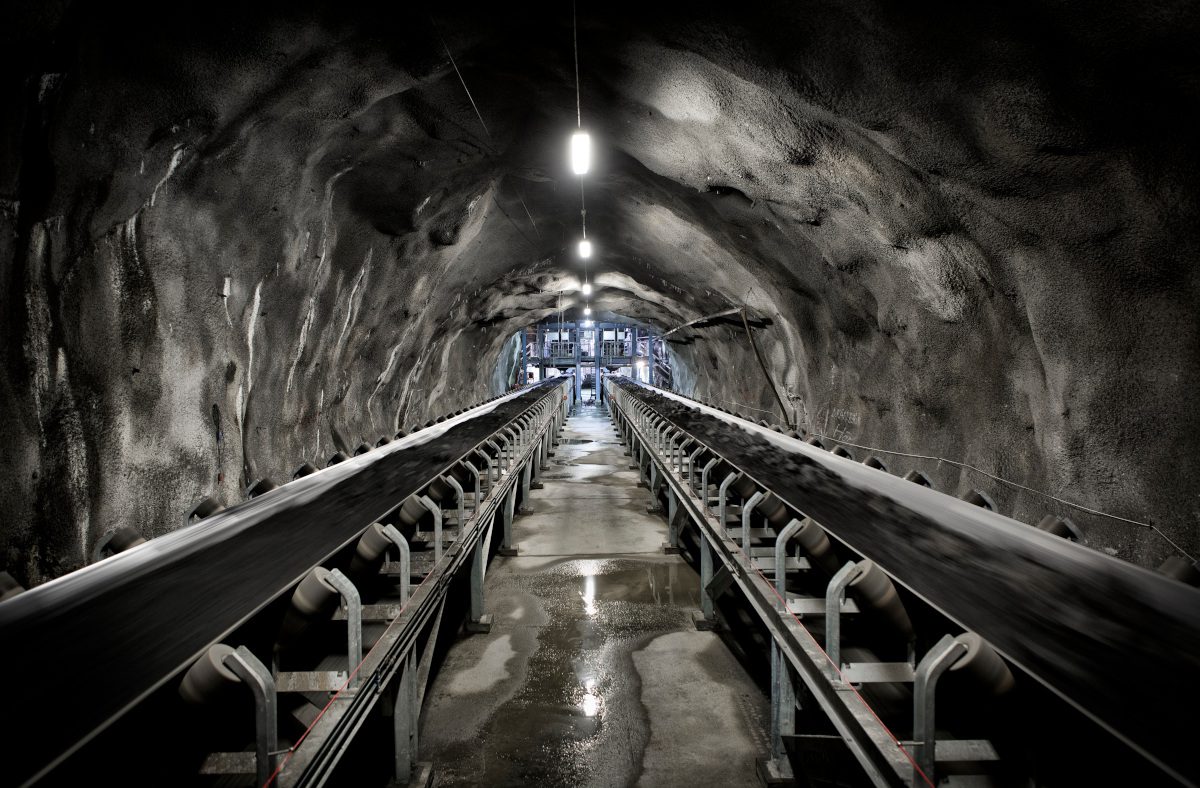
LKAB has awarded ABB a contract to install two ABB Gearless Conveyor Drives (GCDs) on the existing conveyor belt system at its Malmberget mine near Gällivare, Norrbotten County, Lapland, the most northern province in Sweden.
The existing setup already carries up to 15 million tons of iron ore every year, using a 2,800kW wound rotor induction motor (WRIM) with gearbox to drive the conveyor. It will be replaced with ABB’s latest GCD technology, two 1,600kW models with permanent magnet motors (PMM), to enable an increase in annual production while reducing energy consumption per ton.
ABB’s installation engineers and project management team face the challenge of working in a tight space at around 1,250 meters underground to remove the large equipment and replace it with the new units. Once the upgrade is complete in 2025, LKAB will be able to achieve overall energy savings of between 6 and 10 percent, which will translate to considerable OPEX savings per year.
ABB GCDs have a motor power of between 0.2MW and 8MW, removing the need for a gearbox and thereby lowering maintenance costs while improving overall reliability and leading to greater uptime. A unique ABB innovation, they are known to be the most energy-efficient conveyor drive solution.
“We are managing the largest iron ore mines in Europe where productivity must remain high while energy efficiency increases,” said Pär Sundqvist, Engineer and Project Owner, LKAB. “This important upgrade will improve the throughput on the conveyor and help us to meet our energy targets. ABB’s technology will also reduce both OPEX per ton and ongoing lifecycle costs.”
“The new ABB equipment will allow for an improved working environment in the mine – cleaner and safer,” said Ulf Richter, Product Manager Conveyor Solutions, ABB. “Gearless Conveyor Drives are known to be the most energy-efficient solution for conveyors, enabling reliable transportation of ore. The upgrade also means reduced noise and heat in the conveyor drive area.”
The GCD’s PMM are directly coupled to the existing conveyor’s drive pulley and can also adapted to meet the particular demands of this underground installation. The main advantages are energy savings, health and safety improvements, reduced maintenance costs and steady, solid production due to higher reliability.
ABB was awarded the project contract in the third quarter of 2023 and the installation will take place during scheduled maintenance stops with the final commissioning due in August 2025.