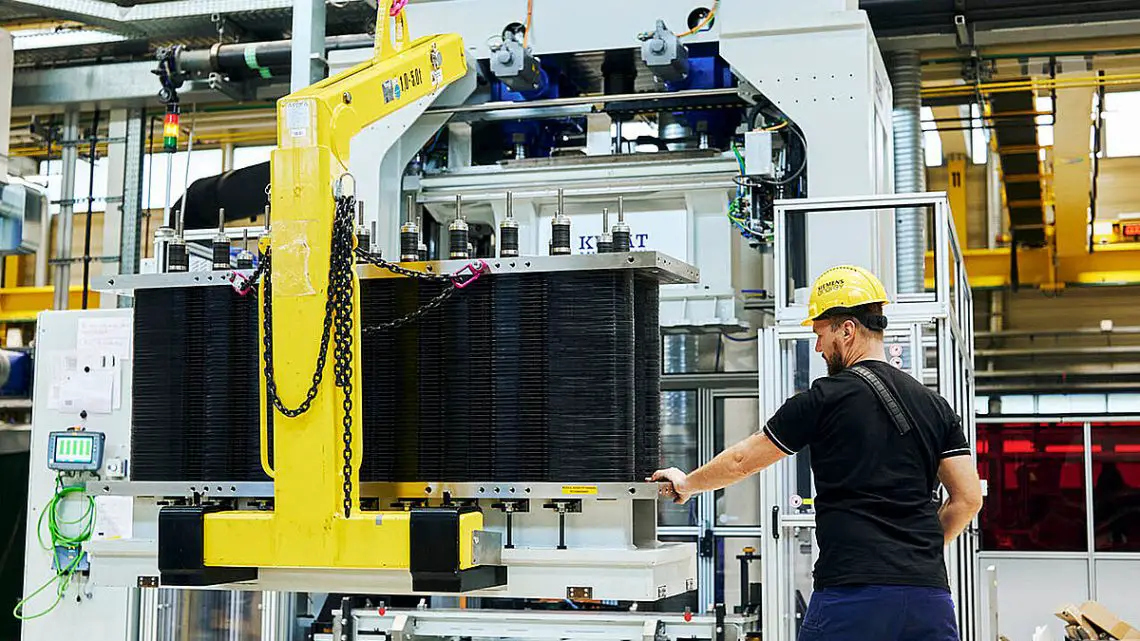
Pump up the volume: Hydrogen hits the big time
November 10, 2023Shifting to mass production is key to producing competitive renewable hydrogen. Partnering with Air Liquide, Siemens Energy is scaling production of electrolyzers using standardization and automation aiming to cut the cost of renewable hydrogen down to size. It’s a development that sits at the heart of the energy transition.
Hydrogen has a key role to play on the road to net zero.
Acting as an energy vector, a storage medium, a raw material for synthetic liquid fuels, and as a gaseous fuel able to address emissions from some of the hardest to abate industrial sectors like steel, chemicals, heavy transport and power generation, hydrogen is vital. Unfortunately, so-called green hydrogen generated using renewable energy is currently too expensive to produce. For this reason, the hydrogen market today is dominated by steam reformation of natural gas, it’s essentially a fossil fuel. However, the imperative of climate change has been amplified by other factors such as security of energy supply concerns that have been greatly increased by the war in Ukraine, for example. This has emphasized the importance of developing a cost-effective renewable hydrogen industry and prompted an acceleration of the market.
Despite the growing interest in renewable hydrogen, the cost has remained an impediment to widespread adoption and displacement of the fossil-fuel derived hydrogen that dominates the current market. The joint venture between Siemens Energy and Air Liquide aims to producing industrial volumes of green hydrogen available bringing economies of scale through the mass production of electrolyzers. The move will not only secure access to electrolyzer capacity but crucially get them at the right price without compromising on safety, quality, and reliability.
Hydrogen Scaling production
Scaling renewable hydrogen production to industrial volumes starts with developing a supply chain that can meet global demand and deliver thousands of megawatts of electrolyzer capacity needed every year. By combining their expertise and efforts, Siemens Energy and Air Liquide intend to do just that with the launch of a gigawatt-scale factory in Berlin. The plant, which heavily relies on automation and robotics to produce electrolyzers in bulk, will initially produce 1 GW of Siemens Energy’s Silyzer 300 Proton Exchange Membrane (PEM) electrolyzer stacks annually. The PEM technology offers a high degree of efficiency and is ideally suited to the variable output that is typical of renewable energy resources. Furthermore, under current plans, this production capacity will increase by at least 1 GW per year, reaching a hefty 3 GW annually by 2025 with a potential for more. In a second step the electrolyzer arrays are being assembled locally, e.g. in the Siemens Energy manufacturing site Muelheim, or in external workshops in the Czech Republic or France or close to future project sites.
Production at the Huttenstrasse facility, located in Berlin’s Moabit district, has just started. The site has so far been known particularly to produce hydrogen-capable gas turbines. The new production line occupies some 2000 m2.
Leveraging Partnerships for Efficient Hydrogen Production
The joint venture expects several benefits, alongside the economies of scale that are translating into a reduction in costs, as has been previously witnessed with renewable energy technologies like wind and solar PV. For example, by partnering with Air Liquide – which is taking a 25.1% equity stake in the JV alongside Siemens Energy’s 74.9% – the gigawatt-scale factory already has a strong business case with a reliable partnership that secures sustained, competitive and reliable product off-take. Both partners able to meet electrolyzer demand arising from their individual portfolios of hydrogen projects.
In addition, in partnering with Air Liquide, Siemens Energy has a strong relationship with a company that has vast experience and deep knowledge of the processes to produce the hydrogen and oxygen, such as hydrogen liquefaction, methanol synthesis, ammonia synthesis, or ammonia cracking.
It is key to long-term success that the Siemens Energy electrolyzer fits the needs of the downstream processes and can also be optimized to better meet those needs in the future. Air Liquide is already working with Siemens Energy electrolyzers deployed at its site in Oberhausen, Germany, in the flagship Trailblazer project. This allows both partners to gather detailed knowledge on how to integrate electrolyzers into an existing plant configuration and learn how to operate the system in combination with existing assets, such as compression and off-take. Sharing know-how, risks and opportunities, the partners aim to rapidly accelerate the transition to affordable renewable hydrogen.
One of the first projects to use stacks from the Berlin multi-gigawatt factory is Air Liquide’s Normand’Hy electrolyzer project. With a capacity of 200 MW, it is the one of the largest PEM electrolyzers currently under development. This project will apply the learnings from Air Liquide’s Trailblazer project in Oberhausen. Other renewable and low-carbon hydrogen projects are also earmarked for development in the Netherlands and elsewhere using the Berlin-produced stacks.
Continuing to cut costs
Within the framework of the partnership, Air Liquide and Siemens Energy have also agreed to dedicate R&D resources to the development of the next generation of electrolyzer technologies. Further efficiency improvements are anticipated, especially given the progress to date.
Siemens Energy started developing hydrogen electrolyzer technology more than a decade ago with a small lab-scale PEM. A commercial product, the Silyzer 200, followed in 2015 with a rated capacity of around 1.25 MW. Although the Silyzer 200 represented a major jump in capacity it was still not suitable for large-scale hydrogen production. That changed with the launch of the Silyzer 300 which has more than 10 times the amount of hydrogen output than the 200 version. Indeed, the Silyzer portfolio scales up by factor 10 every four or five years and sees substantial improvements in efficiency with each generation.
Simultaneously, manufacturing processes have also evolved, from the hand-built Silyzer 100 and 200 to exploring the development of automated manufacturing equipment and implementation of larger scale machines with the launch of the 300. Siemens Energy is also developing manufacturing equipment together with external companies, removing manual processes and increasing automation.
The focus in Berlin is mass production of the existing stacks and a huge step up in production volumes. Increasing production with a factor of 100, within four or five years is only possible in a fully automated large-scale mass production plant of the kind that is being developed in Berlin. Solid investment in manufacturing capacity is enabling the supply chain to invest in capacity growth with confidence too, ramping up from single piece production to mass production in line with stack manufacturing volumes.
In order to cut the specific cost of hydrogen, while mass production of the stacks will take place in Berlin, assembly of the final product will take place closer to the project sites. The Silyzer product contains 24 PEM stacks but built around it are the various ancillaries that are needed for the stacks to operate. These items include the manifolds for the gas, the cooling system, the gas separation system, and the electrical connections among others. In Germany, this stage of assembly will take place at Mülheim but that will change depending on the location of the final project. For the Air Liquide Normand’Hy project, for example, Siemens Energy will work with a French company to produce the skid-mounted electrolyzer array. This approach of working with external partners close to where the final customers are based is key to match the market needs.
Building a hydrogen ecosystem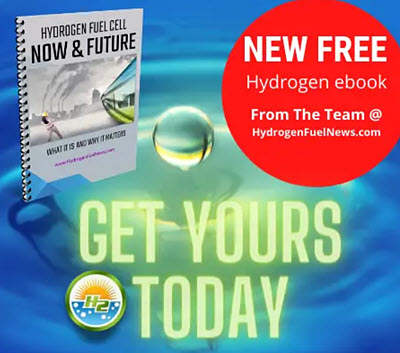
Reasonably priced and affordable renewable hydrogen derived from renewables is a prerequisite for achieving net zero carbon. It is therefore key for our future. By moving into large-scale mass production, the Air Liquide-Siemens Energy partnership is taking a big step towards a cost-effective hydrogen economy using automation and standardization to build economies of scale. At the same time as volumes soar, demand for the electrolyzer business is also rapidly accelerating, rising from approximately 50 or 60 stacks five years ago and increasing by a factor of 10 this year and another factor of 5 to 10 anticipated over the next few years. By fostering a global ecosystem for electrolysis and hydrogen technology, the joint venture is engineering access to industrial volumes of cost-competitive renewable hydrogen. The challenge is global warming, part of the solution is a gigawatt-scale factory.
Muy interesante y valiosa la alianza para producir electrolizadores. Desde el punto de vista de la información habría sido interesante agregar información numérica evolutiva en el tiempo (años), con : Cantidad de electrolizadores producidos por año, Capacidad promedio y total de MW, Inversión en la Alianza, valor de venta de Electrolizadores, etc.
The problem with the production of hydrogen by electrolysis is the cost of the electricity to power the electrolysers, so the question is: where does the electricity for this French project Air Liquide Normand’Hy come from? Is it powered by French grid electricity or from a private source such as a wind farm and/or solar PV panels?
In the UK the fossil-free hydrogen market is being held up by the shortage of low cost hydrogen where most of the electrolysers are powered by expensive grid electricity discouraging the operators of heavy goods vehicle fleets from converting to hydrogen-electric traction, except for some operators of bus fleets and municipal waste collection vehicles that are receiving Government subsidies to reduce their net cost of hydrogen. The high price of grid electricity in the UK set by the twice daily spot price of gas, is holding up the hydrogen economy while giving a strong motivation to producers of “renewable” electricity to build their electricity production; is the balance wrong between motivating producers of renewable electricity and consumers of it, considering that more than 50% of the UK’s electricity is now produced by low cost renewables, not just by expensive gas?
Still many scope to optimize the application of hydrogen. Hydrogen compressor will be important equipment.More important is safety. Many of us has observed the Chinese balloon which they claimed for environmental study but real objective is not yet disclosed