Tesla Battery Day — Has Elon Musk Already “Leaked” The Battery Tech That Will Give Scale To The EV Revolution?
Tesla Battery Day is less than a week away. In my view, most Tesla commentary continues to overlook what is already known when it comes to predictions for what will be revealed on Tesla Battery Day.
Update: Elon Musk has responded to this article:
No, but you make some great points. Important to note that iron’s cost advantage is partly offset by increased pack mass, so the fully considered cost is closer to nickel. That said, iron alleviates much of the scaling problem.
— Elon Musk (@elonmusk) September 17, 2020
While there will no doubt be exciting showcase technology and plenty of “one more thing” elements, Elon Musk has probably already revealed the main battery tech that will enable Tesla to massively scale its mission to accelerate the transition to sustainable energy (and transport).
I analysed and explained my take on this news immediately after it broke during the Tesla 2020 Q2 earning call in July, but it seems a significant portion of Tesla chatter has simply missed it or, more likely, not understood it.
Not everyone knows that LFP battery packs are at least 20% cheaper per kWh than nickel-based battery packs, and that LFP cathodes have no mineral supply constraints or price spikes (unlike nickel cells). But when you do know that, and if you heard what Elon said, it adds up to something very significant.
What did Elon say?
So let’s break it down once more. Here is what Elon already said in the Q2 call for those who didn’t catch it the first time around (this time with italics):
“The real limitation on Tesla growth is cell production at an affordable price, that’s the real limit, so that’s why we’re going to talk a lot more about this on battery day, because this is the fundamental scaling constraint.”
“There’s two general classes of cell, there’s iron phosphate [LFP] and then the nickel based. Nickel based cells have higher energy density so longer range obviously those are needed for something like the Semi where every unit of mass that you add in battery pack you have to subtract in cargo. So it’s very important to have a mass efficient and long range pack.
“However, what we’re seeing with our passenger vehicles is that total vehicle efficiency has gotten good enough that we actually are comfortable having an LFP pack in Model 3 in China, and that will be in volume production later this year. So we think that getting a range that is in the high 200s… you probably get a range of almost 300 miles, with an iron phosphate pack, taking into account a whole bunch of powertrain and other vehicle efficiencies.” Elon Musk, 2020 Q2 Tesla earnings call.
I have written about the economics and properties of LFP cells and nickel-cobalt cells for electric vehicles several times (check here, here, and here), so maybe I have a different perspective from most Tesla watchers. The interpretation of Elon Musk’s statements seems unambiguous to me. But even simple words are open to different interpretations, so I’ll spell out my interpretation here:
There are lots of varieties of electrochemistry, but currently there are only two main commercial pathways for EV cells, LFP (iron phosphate–based cathodes) and nickel (nickel cobalt–based cathodes). This is widely understood within the industry. So far, so good.
The higher energy density of nickel-cobalt cells (compared to LFP) is well suited to long-range, weight-sensitive electric vehicles like the Tesla Semi. However (in contrast) for Tesla passenger vehicles (especially the entry level vehicles not needing 400+ miles of range, or crazy power-to-weight performance ratios), Tesla’s many years of accumulating powertrain and other efficiencies mean that even the more modest energy density of LFP is now sufficient to give almost 300 miles of range.
Add in the crucial side note (that Elon knows very well but most of the Tesla community apparently does not) that LFP EV batteries are much cheaper per kWh and much more scalable (raw material availability) than nickel ones.
Conclusion: we are now at a point where the lowest-cost EV battery technology, LFP, despite its lower energy density, has enough energy to power Tesla’s highest-volume entry level vehicles with a range of close to 300 miles.
Tesla is not going to unlearn all the vehicle efficiency technologies it has gained, it will only improve them further. LFP is not going to get less energy dense with time (it will improve further). LFP will not increase in price / kWh (it will get cheaper). Therefore, all of Tesla’s future most affordable entry level vehicles will also get very decent range (enough range for mass market acceptance) by using LFP batteries, at a low cost.
In short: LFP is by far the cheapest and most scalable (in production volume) EV battery chemistry that exists today and for the foreseeable future, being at least 20% cheaper ($/kWh) at the pack level than nickel-cobalt battery packs. If LFP is now a suitable technology fit for Tesla’s highest sales volume vehicles, it would be crazy of Tesla not to use LFP.
True, LFP does not have the highest energy density. True, it doesn’t have the image of the most glamorous or sexiest battery tech out there. But don’t let appearances fool you — it is precisely LFP’s low cost and potentially massive production scale that the EV revolution needs in order to displace combustion engine vehicles. And killing off the internal combustion engine in the age of global heating, pollution, and dysfunctional fossil fuel politics is sexy as hell.
To satisfy the mass market, EVs don’t need extreme range, they need low cost, and higher manufacturing volume
The 2012 Tesla Model S was already capable of 265 miles of rated range and 35 minutes of charging for decent onward journey progress. The 2017 Tesla Model 3 was already capable of around 300 miles of range and 20 minutes of charging for decent onward progress. These vehicles already had sufficient technical capabilities to replace combustion engine vehicles for a large proportion of car buyers, but were held back from true mass market demand by their price points. To reiterate Elon’s first point quoted above:
“The real limitation on Tesla growth is cell production at an affordable price.”
The technical capabilities for the broad acceptance of EVs are in place, but mass market dominance requires lower prices than EVs have been offered at up till now. Battery packs are by far the most costly single component of EVs, and so reducing the battery cost is key.
For a bit more color on what constitutes mass market vehicle pricing, the top selling models in Europe for each of the past 3 years have been the VW Golf (Germany prices from €19,881 including tax), the Renault Clio (€13,540), and the VW Polo (€15,138). That’s an average of around €16,200 ($19,265) — which is, by definition, mass market pricing in Europe.
In the US, putting to one side the outlier culture around pickup trucks (a segment Tesla is soon addressing), the best sellers are the Toyota RAV4 (starting $25,850 before sales tax), Nissan Rogue ($25,200), and Honda CR-V (~$25,000). That’s an average around $25,350 (€21,300) plus tax, so a good bit higher than in Europe (partly due to average US folks preferring these significantly larger vehicles).
Yes, savvy folks know that an EV will save them at least €25,000 in fuel costs in Europe over a life of 150,000 miles / 250,000 km (and save a bit less in the US due to lower fossil fuel prices), but unfortunately most consumers think about the costs in lump sum amounts, not in flow rates over time. Despite the substantial lifetime savings, the upfront sticker price of EVs needs to come down to close to the above price points in order to gain higher mass market appeal. LFP, being by far the most cost-effective EV battery technology, is the most direct way to get the price of EVs down.
As time goes on, the efficiency of EVs will keep improving ever further, requiring less battery energy to deliver competent and convenient range. LFP’s key characteristics of low cost and manufacturing supply will keep improving further, and as a welcome side bonus, LFP’s technical capability will improve further (indeed, that’s a big part of cost reduction per kWh). So LFP is going to become an ever better fit for mass market EVs over time.
Precisely these dynamics led to the arrangement between Tesla and battery maker CATL to supply LFP cells for its Shanghai Gigafactory Model 3, news of which broke in February 2020. Reportedly, the two had been talking about LFP supply for “more than a year” beforehand. That tells us that Tesla has been thinking about LFP for a long time already.
What’s behind the cost advantage of LFP?
I’ve done several analyses of the capabilities of LFP batteries in relation to the traditionally more common nickel-cobalt EV batteries if you want to understand more about that. The short story is their relative cost. Mined nickel and cobalt mineral supply (for nickel-cobalt cells) is only available at a fraction of the scale of mined iron and phosphate supply (for LFP cells), and the former minerals are much more expensive.
Even the lithium hydroxide that nickel batteries need is more expensive than the lithium carbonate the LFP batteries need, though this isn’t a major cost component overall. Nickel-cobalt EV batteries are already taking most of the world’s current cobalt supply, and unless mined mineral volume can change very fast, will take most of class 1 nickel too once EVs approach 20% to 25% of global auto market share (they will hit ~10% share in Europe this year).
Over time, both nickel and cobalt can steadily be mined more extensively, but mining projects have a very long lead time, and the mineral supply squeeze is already setting a looming cost floor for how cheaply nickel-cobalt batteries can be made in the medium term, and obviously setting limits on the quantities in which these batteries can be made. Nickel-cobalt chemistries still work out around $100/kWh at the pack level, even for the highest volume contracts from the lowest cost suppliers.
LFP avoids all these constraints due to the relatively huge abundance of the constituent minerals currently mined (iron, phosphate and, increasingly, trace manganese) and consequently the low mineral pricing. LFP has already reportedly achieved $80/kWh at the pack level, and still has potential to come down much further over time since it is nowhere near the mineral cost floor. LFP’s mineral components are so abundant that even when almost all vehicles sold are EVs, there will be more than enough minerals to supply the batteries required.
LFP’s cost advantage has even more relevance for stationary storage batteries, where the slightly higher weight of LFP over nickel-cobalt is typically not an issue. Stationary storage economics mostly depends on low cost and high cycle life — there are common varieties of LFP which can meet both of these requirements far better than most other traditional battery chemistries. We can expect that most of Tesla’s stationary storage will take advantage of this, and eventually switch to LFP.
Nickel-cobalt will continue to have an important role for Tesla’s halo/showcase products
As should be clear by now, nickel-cobalt batteries are not as cost competitive, but have energy density advantages over LFP batteries, and they have more room to gain (and more quickly gain) in energy density in the future. Given the discussion above, obviously, this higher energy density is no longer strictly required for capable-enough-for-mass-market electric vehicles, and struggles to compete with LFP on cost, for this class of vehicles.
However, the energy density advantage of nickel-cobalt will remain very relevant for halo battery electric products like very long range EVs (over 300 miles or even 400 miles), and high performance EVs where relative light weighting is still very desirable. This obviously includes Tesla’s semi trucks, where vehicle weight inversely correlates with available cargo payload, as Elon set out above.
Tesla’s Roadrunner battery project
In March 2020, an environmental study document surfaced relating to a novel Tesla battery project. The document described proposed construction works at Tesla’s facilities in the Kato road area of Fremont “To accommodate new battery manufacturing equipment and R&D space (known as ROADRUNNER).”
Tesla has not yet spoken about the project publicly, but this will almost certainly play a major role as a high-end technology showcase at battery day. The study document reveals the following details:
- The construction of 29,475 sq feet of manufacturing and R&D space at Kato road building, plus some additional existing space at the adjacent Page building.
- At least 400 new production employees, with shifts of 100 employees working at any given time.
- An additional 200 MWh per day of electrical supply to support the project: for traditional battery production methods, this would be enough for around 3,000 kWh of battery production per day (equivalent to 11,000 units of 100 kWh packs per year). But the point of Roadrunner is to implement new approaches to efficient cell manufacturing, like Tesla’s energy-efficient dry electrode production process, which doesn’t need solvent drying ovens. This and other innovations may mean substantially more cell production in this facility. Perhaps 20,000 units of 100 kWh, per year.
- Declaration of both nickel-cobalt-aluminium and nickel-cobalt-manganese materials (amongst others) on site, suggesting both of Tesla’s existing nickel-cobalt cathode variants will be produced. Materials declarations give no indication of LFP cathode variants being produced as part of the Roadrunner project.
As of a month ago, the Roadrunner main construction work was nearing completion. Since this is the first record we have of Tesla producing its own in-house cells at a commercial volume, and R&D is part of the intention, we have to imagine that the company will incorporate its Maxwell Technology subsidiary’s dry battery electrode production process.
Tesla will also presumably use the Hibar subsidiary’s electrolyte filling technologies.
Another rumored recent acquisition, SilLion, will be leveraged to optimize the silicon content in the graphite anodes, without excessive swelling and mechanical stress, to improve energy density.
The work of the Jeff Dahn research group at Dalhousie University will be leveraged to optimize electrolyte doping. They’ve also been working on single crystal cathode technology (see million-mile battery, below) and other chemistry improvements, mostly aimed at optimizing cycle life.
There’s also Tesla’s tabless electrode technology, that we already know of via a May 2020 patent application. This will reduce ohmic resistance of the current flowing inside the cells, and thus significantly reduce heat generation, improve cell longevity, reduce/simplify cooling needs, and reduce the energy needed for cooling. It will also make the cells more tolerant of high power charging (as well as discharging), and thus reduce Supercharging time as well as improving peak power output. This is quite a big one:
Way more important than it sounds
— Elon Musk (@elonmusk) May 7, 2020
Along with all of these, there are very likely a few other battery technology innovations, and manufacturing innovations, Tesla will be employing in this production line that we don’t yet know about. Recent leaks suggest the diameter of the Roadrunner cells is around double that of 2170 cells. If so, this should increase the energy density at the cell level, as well as simplifying pack internals and assembly, reducing packaging cost.
It is clear that Tesla intends this Roadrunner battery project to produce cutting edge cells in terms of energy density, power density (C-rates of both charge and discharge), thermal performance, and cycle life also. Presumably, Tesla intends to prove out new methods in manufacturing efficiency (speed, energy, capital cost, yield), and thus also improved $/kWh cost of cells (compared to existing commercial nickel-cobalt cells).
Applications for Tesla’s Roadrunner battery cells
Since the Roadrunner cells will most likely quickly become the highest energy density available to Tesla at commercial volume, the company will almost certainly be deploying them in cutting edge applications. Logically, these applications will be the forthcoming Semi Truck and the Roadster, and the upcoming Plaid Tesla Model S and Model X.
I think Tesla will announce the availability of these Plaid models on Battery Day, since Porsche has recently tweaked the 2021 Taycan for more performance and Lucid Motors has also announced a high performance challenger arriving next spring.
In order to head off another upcoming extreme long range challenger from Lucid, Tesla may also announce an ultra long range variant of the Model S with a ~130 kWh Roadrunner battery which should achieve a Lucid-beating 525+ mile EPA rating (or more). The cell energy density improvement will make the weight gain minimal.
Since initially the Roadrunner cells will be expensive to produce and available in only moderate volumes, these near-term Plaid and ultra long range vehicles will command high prices commensurate with their exclusivity and initially limited production volumes. Before long we can expect further ramp up of production of Roadrunner cells, likely in some portion of Tesla’s gigafactories; very likely in Texas where the Tesla Semi and Cybertruck will be produced. The Plaid version of the Cybertruck may use the Roadrunner cells. Tesla may also work with Panasonic at Gigafactory Nevada to produce Roadrunner cells. More on how Tesla may scale up Roadrunner cells below.
The final “application” for the Roadrunner technology is simply to help Tesla diversify its strategy and strengthen its bargaining position.
Diversity, flexibility, and strategic bargaining position
We have seen that even modest energy density LFP cells will power very compelling yet affordable vehicles, which will become Tesla’s best sellers by volume. Tesla may also be able to bring some of its battery technologies — like dry electrode, tabless electrode, and electrolyte doping — to bear on LFP cells, perhaps in partnership with CATL, perhaps ultimately with its own LFP production. Tesla will meanwhile continue to find good uses for their existing cells with decently high density. These are the Panasonic NCA cells that supply “Long Range” and “Performance” vehicles, and LG’s NCM cells that power Tesla’s Long Range Model 3s and soon Model Ys in China.
Since Tesla’s highest volume vehicles are so efficient that they can make use of fairly generic cells from any available supplier, the company can shop around pretty much anywhere to ensure it is benefitting from the most competitive prices on the open market. This puts Tesla in a good spot to negotiate the most competitive contracts, potentially with a wide range of suppliers.
Add to that available palette the in-house Roadrunner cells, which ensures that Tesla is not dependent on anyone else’s technology to maintain its reputation for being at the cutting edge of halo electric vehicles and frontier applications (like long-range Semi Trucks), and Tesla should be in a strong position.
Related to the non-dependence point, this flexible strategy, drawing on diverse types of cells, allows Tesla to hedge against the vagaries of the mineral supplies and cost fluctuations, especially those for nickel and cobalt. Having access to a stable low-price technology like LFP means that Tesla’s core business of making and selling ever higher volumes of battery electric vehicles and battery energy products is shielded from these fluctuations and potential bottlenecks.
This diversified and flexible approach to cell supplies has long been in the works for Tesla. As Drew Baglino said in the 2019 annual meeting, in regard to Tesla needing a large-scale solution to battery cell production, “We are not sitting idly by, we’re taking all the moves to be masters of our own destiny here, technologically and otherwise.”
“Million-mile” battery
Since at least 2015, Elon Musk has referred to Tesla’s plans to achieve EV powertrains with “a million miles” of useful life, including eventually for the batteries. This obviously depends on how many miles a battery’s charge cycle enables, and the number of charging cycles the cells can perform before significantly degrading.
If a battery enables a vehicle to have 400 miles of range, then 2,500 cycles gives you a million miles. 300 miles of range requires ~3,333 cycles, and so on. The cutoff point in defining “useful life” (or “significant degrading”) is typically when the battery pack still retains at around 70% of its original energy capacity. Even below 70%, the battery and its cells will still be valuable for less energy dense uses, such as in stationary storage applications.
The Jeff Dahn research group has worked on bringing nickel-based cells up to 4,000 to 6,000 cycles in the lab, using single crystal cathode particles and custom electrolytes. Commercial production versions would have to balance cycle life with other characteristics, but should be able to get to the 2,500 to 3,000 cycles to claim “a million miles.” Maxwell has reported that its dry electrode manufacturing technology also increases cell cycle-life.
There are only a couple of high-use cases where a million-mile capability would be obviously useful — Tesla’s semi trucks and robotaxis. Most privately used vehicles almost never get too much over 300,000 miles of lifetime use (which Teslas can already provide), requiring over 20 years of average driving duty (13,500 miles per year for typical US drivers). A private vehicle is also well behind the curve on safety technology (and other features) when 20 years old, even if its powertrain is in perfect condition.
As we covered above, LFP isn’t a good fit for weight sensitive applications like the Tesla Semi, so despite some varieties of LFP working beyond 2,500 cycles already, the Semi will use nickel-based versions of a “million-mile battery.” An LFP version would be more cost effective in robotaxis. Note that Tesla’s existing LFP cell supplier partner CATL has already announced its own “million-mile battery,” but has said this technology neither uses conventional LFP nor nickel-based cathodes.
How to scale battery production in practice?
The Kato road facilities will probably only supply around 10,000 to 20,000 units of 100 kWh battery packs, or equivalent, per year. This will be okay in the short term if only the Plaid S and X, ultra long range S and X, and initial units of the Tesla Semi need to be supplied. But each Semi will probably use at least 800–1000 kWh of cells, so when these vehicles scale beyond a few hundred units per year, the Roadrunner battery production will have to scale up. And that’s before even considering a Plaid Cybertruck and the Roadster.
This scale will likely take place in some portion of Tesla’s new gigafactories (Shanghai, Berlin, and Austin), but likely Roadrunner may not be the exclusive gigafactory cell type. Panasonic’s classic NCA cells will continue to be produced at Gigafactory Nevada, and depending on what supplier relationships Tesla has negotiated, it’s quite possible that Tesla will also have lines making its own LFP cells, or partner on those lines with CATL.
The in-house vs supplier part of the story is difficult to predict, since some of Tesla’s strong strategic negotiating position, highlighted above, can be achieved by just having modest in-house cell production, flexible cell needs, and varied arrangements with outside suppliers.
However, if Tesla’s Roadrunner cells work out as cost efficient and high performance as they are planned to be, it would only make sense for Tesla to ramp up the manufacturing capacity, since they will likely be the most cost competitive nickel cells available. Bear in mind, though, that the potential nickel and cobalt mineral supply issues mentioned above mean that Tesla will look to avoid over-dependence on any cell type beyond LFP, unless Tesla can get very reliable, stable in price, and massively scalable mineral supply agreements in place.
Some such mineral supply contracts will be necessary for even the modest Kato road production of Roadrunner. The scale of those contacts is something to watch for on Battery Day to indicate the volume of Tesla’s roadrunner plans.
Even if Roadrunner goes to plan, as noted above, LFP (since it can also benefit from some of the same novel manufacturing techniques) will still have the cost advantage and ideal fit for the entry level vehicles. Again, in my view, LFP is Tesla’s route to true mass market sales volumes, and fully disrupting sales of internal combustion engines.
Other Tesla Battery Day technologies?
What are some of my more off-the-wall thoughts on what might arrive at Tesla Battery Day?
It might be sensible to put a small 50 kg (around 1 kWh) Maxwell supercapacitor bank into the Plaid Model S (and a future Roadster) for battery/motor cooling benefits during hard track sessions.
Why? Repeated extreme acceleration and regen adds a lot of battery pack heat (and motor heat). The limiting factor for performance EVs on race tracks is not power or performance, but heat buildup and thermal throttling to protect components. A small supercap cache that shaves off 50% of the battery’s load for the hundreds of acceleration/regen tasks (e.g., hundreds on a single lap of the Nürburgring Nordschleife) would make a huge difference to controlling battery pack temperature, and allow more cooling to go to motors and inverters.
Since this simply passes the buck (and the supercapacitors likely get hotter than the batteries due to lower round trip efficiency), the feasibility of this is dependent on how heat tolerant Maxwell’s supercapacitors are. I will also concede that if the tabless electrode design of the Roadrunner cells works exceptionally well, extreme battery heating may be significantly mitigated anyway. This would remove any advantage of a supercap cache.
We already know that the Model Y’s heat pump and octovalve will eventually make their way to all other Tesla vehicles, since Elon referred to this when discussing “our passenger vehicles” and efficiency, above.
The Tesla Semi will likely not yet be announced as production ready, but we may see a formal update announcement on it — rising in range to 600 or more miles perhaps, thanks to the Roadrunner cells.
Tesla’s V3 Superchargers are officially rated for 500 volts, and the vehicles currently have power systems at 400 volts. At some point we will probably see the higher end Teslas migrating to a 500 volt system design. Otherwise, why the gain in Supercharger voltage capability? Tesla Battery Day may be a good time to announce that, or it may come later.
An aesthetic refresh may come to the Model S and X, and a modest external refresh will obviously be somewhat necessary for the Plaid versions anyway, given their wider stance and large air diffusers.
We know that smaller and more affordable Tesla models will come in the future, but I don’t see any announcements on these happening for another year or so, partly because they may Osborne orders and sales of the Model 3 and Model Y. These future smaller Tesla models may actually only be properly announced once they are available to order. Remember how the Model Y was unveiled in a fairly low-profile event, for fear of Osborning Model 3 sales, and production started quietly? This may be even more the case for these future mass market models.
Conclusion
In my interpretation, knowing the cost advantages of LFP packs over nickel-cobalt battery packs, Elon’s words on the Q2 2020 earnings call were clear. Tesla’s entry vehicles, with close to 300 miles of range, will move to cost effective LFP technology. These will be Tesla’s highest sellers globally, because almost 300 miles of range is enough for most consumers, and once that’s included, it is competitive pricing that is the key factor in scaling. Tesla will look to source these from CATL, but may also begin to produce them in-house in partnership with CATL or other LFP suppliers. Some of Tesla’s general battery technologies should be applicable to LFP and may further reduce costs.
Tesla’s Roadrunner nickel batteries will incorporate all of Tesla’s battery technologies and break new ground in overall performance terms. These will enable Tesla’s cutting edge vehicles to stay well out in front in headline performance, range, charging, and longevity specifications. They will also become the most cost competitive nickel-based cells that Tesla has access to. Tesla will keep Roadrunner in-house or in tight manufacturing partnerships (Panasonic and/or LG), and gradually expand Roadrunner production volume in Austin, Berlin, and possibly the other Gigafactories.
Having this two-pronged novel approach to cell supply, at least one of which will be in-house, in addition to the existing Panasonic and LG arrangements, gives Tesla flexibility and puts the company in a strong strategic position regarding negotiations and supply contracts.
I think these are the key parts of the picture, but I’ve probably missed some other obvious things, and hopefully there will be some surprise “one more things.” Please jump into the comments to share your thoughts.
Have a tip for CleanTechnica? Want to advertise? Want to suggest a guest for our CleanTech Talk podcast? Contact us here.
Latest CleanTechnica.TV Video
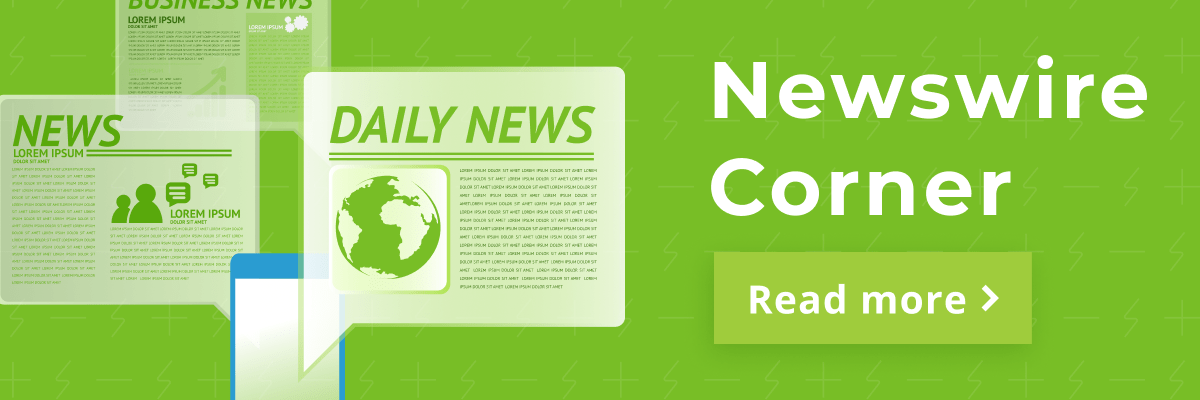
CleanTechnica uses affiliate links. See our policy here.